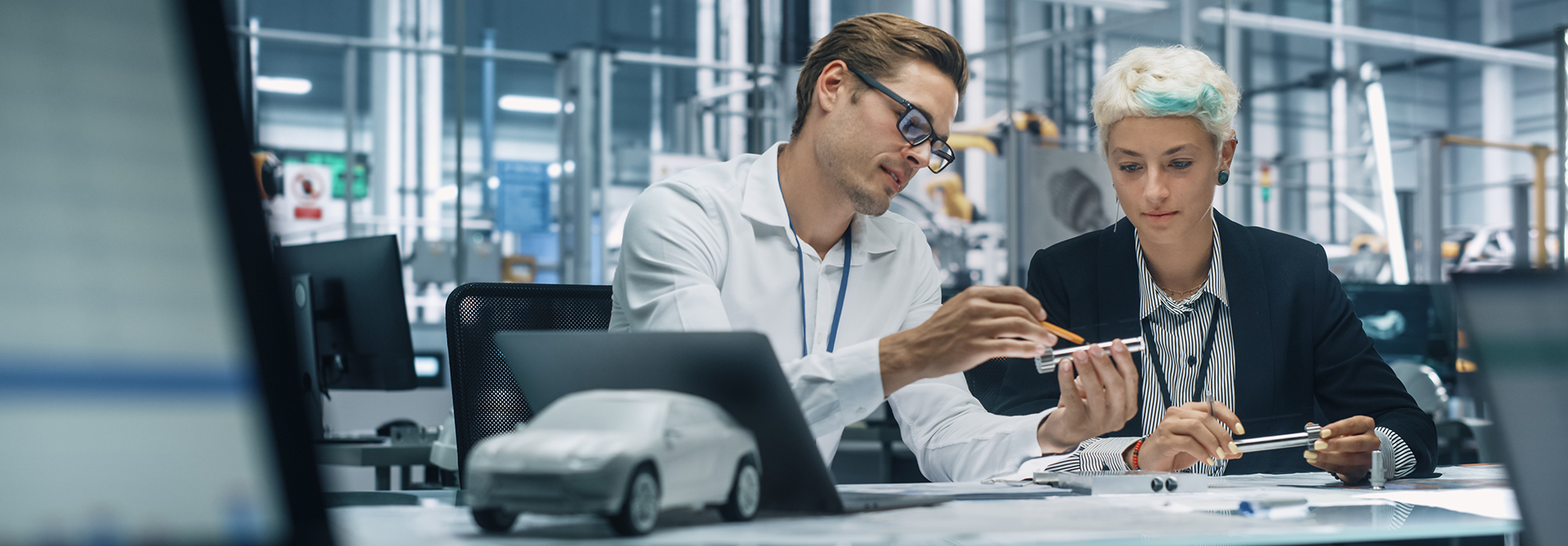
UMFASSENDE SQA STATT WARENEINGANGSKONTROLLE VON GESTERN
Die Bedeutung einer fehlerfreien Zulieferung ist in der modernen Automobilproduktion unumgänglich. Die Zeiten der Wareneingangskontrolle gehören der Vergangenheit an. Heutzutage werden die Komponenten idealerweise direkt an die Fertigungslinie geliefert – und das in der exakten Reihenfolge, wie sie für die jeweilige Fahrzeugvariante benötigt werden. Schließlich können Mängel an den gelieferten Teilen dazu führen, dass diese nicht verbaut werden können. Im schlimmsten Fall muss in solchen Situationen die Produktion sogar gestoppt werden, falls keine sofortigen Gegenmaßnahmen ergriffen werden können.
Damit solche Vorfälle von vornherein vermieden werden können, ist die Qualitätssicherung der Lieferanten (auch Supplier Quality Assurance, SQA) bereits im Vorfeld einer Projektvorbereitung involviert: beim Sourcing, also der Auswahl der Lieferanten. Je nach Projekt gibt dabei der auftraggebende Hersteller die Lieferanten vor. Oder die Lieferantenauswahl wird vom Auftragsfertiger selbst vorgenommen – natürlich in Abstimmung mit dem Auftraggeber, der die Entscheidung absegnen muss oder sich zumindest ein Veto-Recht ausbedingt. Welcher Lieferant in Frage kommt, entscheidet sich nach Maßgabe des Lieferanten-Ratings. Dieses wird auf Erfahrungen und Bewertung bei zurückliegenden Projekten erarbeitet und kennt grundsätzlich die drei Stufen Grün, Gelb und Rot. Selbsterklärend wird mit „rot“ bewerteten Lieferanten nur dann zusammengearbeitet, wenn beispielsweise der Kunde darauf besteht.
SOURCING IN GEMEINSAMEM MITEINANDER VON EINKAUF UND SQA
Der Einkauf hat die Aufgabe, den besten und günstigsten Lieferanten zu finden – und zwar unter Berücksichtigung der Gesamtkosten, also einschließlich der Logistik- und sonstigen Zusatzkosten sowohl in monetärer als auch in ökologischer Hinsicht. SQA hat die Aufgabe herauszufinden, ob der Zulieferer, der ein Angebot für ein bestimmtes Bauteil abgibt, dieses auch wirklich herstellen und zuverlässig in der benötigten Stückzahl und in fehlerfreier Qualität liefern kann.
Dazu wird bereits ganz am Anfang des Projektes eine Source Evaluation beim Lieferanten durchgeführt. Diese beurteilt, ob der betreffende Lieferant aus Qualitätssicht – etwa aufgrund von vorherigen Erfahrungen – in Frage kommt oder nicht. Dabei reicht es nicht, sich damit zufrieden zu geben, dass der Lieferant nach ISO zertifiziert ist. Denn das beweist nur, dass er über die nötigen Basiswerkzeuge für ein umfassendes Qualitätsmanagement verfügt. Vielmehr beurteilt die Source Evaluation, wie er diese Instrumente nutzt, um seine eigene Qualitätsperformance zu messen und zu überwachen.
Dabei ist es unverzichtbar, sich den Betrieb wirklich anzusehen: Wo plant der Lieferant die Fertigung? Auf welchen Anlagen wird gefertigt? Wie wird dort gearbeitet? Eine reine Beurteilung auf Grundlage von Unterlagen, wie sie von einigen Dienstleistern ohne direkte Vor-Ort-Prüfung angeboten wird, kann dies nicht zuverlässig leisten.
ENGE UND VERTRAUENSVOLLE ZUSAMMENARBEIT MIT DEN LIEFERANTEN - VON ANFANG AN
Sobald der Lieferant nominiert ist, werden in enger Zusammenarbeit des Auftragsfertigers mit dem Lieferanten die näheren Details ausgearbeitet. Prozesse beim Lieferanten werden im Zuge der Qualitätssicherung genau durchleuchtet. Das kann im Einzelfall auch bedeuten, dass bei kritischen Teilen einzelne Aspekte im Design des Teils bzw. des Werkzeugs geändert werden. Damit gewährleistet man die Prozesssicherheit, beispielweise wenn man bei einem Rohbauteil noch Radien vergrößert, um Ausdünnungen zu reduzieren bzw. Ziehrisse zu vermeiden. Dies kann jedoch immer nur im Zusammenspiel mit der Entwicklung umgesetzt werden. Deshalb ist die SQA schon von Beginn an essenzielles Mitglied im Entwicklungsteam.
Ziel ist, den Lieferanten bis zum SOP (Start of Production), also dem Beginn der Serienproduktion, so weit zu bringen, dass er die benötigten Stückzahlen herstellen kann und die Qualität der Teile den Erwartungen entspricht. Dazu wird in der Vorbereitungsphase immer wieder nachgeprüft, ob etwa die betreffenden Anlagen schon aufgebaut sind und eingefahren werden, ob der Werkzeugbau entsprechend der vereinbarten Terminschiene vorankommt. Oder auch, ob man beispielsweise das Personal schon entsprechend geschult und trainiert hat. Das erlaubt in aller Regel eine zuverlässige Prognose, ob der Lieferant zum SOP so weit ist, wie es der Zeitplan erfordert.
RELATIONSHIP BUILDING – LIEBER MITEINANDER ALS GEGENEINANDER
Allerdings gibt es Fälle, wo sich zusätzliche Hindernisse in den Weg stellen. Etwa, wenn vorgezogene Lebensdauertests ergeben haben, dass noch technische Änderungen an Bauteilen erforderlich sind. Denn das bedeutet, dass auch die Werkzeuge nochmals geändert werden müssen. In solchen Situationen hat ein erfahrener Auftragsfertiger, der bereits mehrere erfolgreiche Projekte der Automobilproduktion mit dem betreffenden Lieferanten durchgeführt hat, einen klaren Vorteil gegenüber einem weniger erfahrenen Qualitäts- oder SQA-Dienstleister. Der erfahrene Auftragsfertiger strebt eine enge Kooperation mit dem Lieferanten an, anstatt lediglich den Druck zu erhöhen.
Wenn der ausgewählte Lieferant oder einer seiner Unterlieferanten mit Herausforderungen konfrontiert ist, strebt man gemeinsam nach einer Lösung durch eine vor-Ort-Betreuung. Gerade in solchen schwierigen Situationen ist eine offene Zusammenarbeit unerlässlich. Der Auftragsfertiger bringt dabei seinen langjährigen Erfahrungsschatz, seine Geduld und sein Durchhaltevermögen ein. Da die Zusammenarbeit mit Lieferanten in der Regel langfristig angelegt ist, ist es von großer Bedeutung, dass beide Parteien erhobenen Hauptes aus einer solchen Krisensituation herausgehen können.
KURZFRISTIGER LIEFERANTENWECHSEL IST IN DER REGEL KEINE OPTION
Die gemeinsame Kraftanstrengung ist letztendlich alternativlos, um den Anlauf trotz möglicher Probleme zu bewerkstelligen. Ein Lieferantenwechsel in letzter Minute gestaltet sich äußerst schwierig, da keine verfügbaren Anlagen und Werkzeuge bei einem anderen Partner zur Verfügung stehen. Zudem erfordert ein Lieferantenwechsel eine langwierige Vorbereitungszeit, da man alle Tests erneut durchführen muss.
In der Regel ist es kaum möglich, diesen Wechsel innerhalb eines kurzen Zeitraumes zu realisieren. Ab einem bestimmten Zeitpunkt befinden sich also Fertigungsbetrieb und Zulieferer in einer Art Schicksalsgemeinschaft: Auftretende Problem müssen zusammen durchgestanden werden, um das gemeinsame Ziel zu erreichen.
Höchste Priorität hat dabei die fehlerfreie Lieferung der Teile, da man eine Wareneingangskontrolle lediglich bei Auftreten eines Problems durchführt. In solchen Fällen müssen die Teile kontrolliert, sortiert oder im schlimmsten Fall nachgearbeitet werden, was Zeit und Geld kostet. Daher ist es für einen reibungslosen Ablauf unerlässlich, bereits im Vorfeld gemeinsam mit dem Lieferanten Maßnahmen zu ergreifen, um sicherzustellen, dass fehlerfreie Teile an die Produktionslinie geliefert werden. Gleichzeitig ist es wichtig, dem Lieferanten bewusst zu machen, dass man ihn nicht nur fördert, sondern auch nach einem erfolgreichen Serienanlauf weiterhin fordert. Nur diejenigen, die sich in der Qualitätssicherung bewähren, kommen auch für zukünftige Projekte in Betracht.
KLARE QUALITÄTSVORGABEN, GENAUE KONTROLLEN
Außer den konstruktiven Vorgaben, die schon beim Start des Projektes festgelegt werden, müssen die angelieferten Teile vor allem Haltbarkeitstests bestehen: von der mechanischen Haltbarkeit über die Montier- und Zerlegbarkeit bis hin zur Widerstandfähigkeit gegenüber klimatischen Einflüssen. Unterschieden wird hier, wie üblich, zwischen der Null-Kilometer-Qualität (also der Beschaffenheit der Teile zum Zeitpunkt des Einbaus; Zero Mileage Quality) und der Feldqualität, der Haltbarkeit und Funktionssicherheit beim praktischen Einsatz im Fahrzeug.
Ein wichtiger Punkt bei der Zero Mileage Quality steht beim Start des Projektes, also der Sourcing-Phase, noch nicht im Detail fest: die geforderten Toleranzen, also die erforderliche Fertigungsgenauigkeit. Diese wird erst im Laufe des Entwicklungsprozesses festgelegt. Ob die Beschaffenheit der Teile den Anforderungen entspricht, muss der Lieferant durch geeignete Tests überprüfen. Mit der positiven Erstbemusterung bestätigt der Lieferant, dass die Bauteile die Anforderungen erfüllen. Die Prüfgebiete der Erstbemusterung werden durch den SQA bestätigt.
Zudem wird relativ zeitnah vor dem SOP eine Prozessabnahme im Zulieferbetrieb durchgeführt. Hierbei fertigt der Lieferant im Beisein eines oder mehrerer SQA-Spezialisten einige Stunden lang oder eine bestimmte Anzahl von Teilen. Diese werden dann vermessen und geprüft. Durch solch eine Vorgehensweise stellt man praxisgerecht unter Beweis, ob das Personal angemessen geschult ist, ob die Anlagen geeignet sind und ob die Prüfung und Vermessung der Teile reibungslos funktioniert. Somit lässt sich sicherstellen, dass die gesamte Produktion prozesssicher und zuverlässig abläuft.
WENN TROTZDEM ETWAS PASSIERT: DAS PROZEDERE IM FEHLERFALL
Während der laufenden Serienproduktion erfolgt eine Qualitätsüberprüfung, beim Verbau der Teile an der Fertigungslinie durch die Werkerselbstkontrolle. Lässt sich das Teil nicht wie gewöhnlich einbauen oder fallen an ihm sichtbare Mängel auf – etwa ein Kratzer – melden das die Mitarbeitenden sofort. Anschließend wird eine Untersuchung durchgeführt, um festzustellen, ob weitere Teile aus derselben Lieferung ähnliche Fehler aufweisen. Falls dies der Fall ist, sortiert man die gesamte Lieferung vor dem Einbau weiterer Teile. Der Lieferant wird über einen Claim informiert, um die Ursache des Mangels selbst zu untersuchen.
Solange der Lieferant keinen Clean Point meldet, also die erfolgreiche Beseitigung des aufgetretenen Problems, werden alle Lieferungen einer Durchsortierung unterzogen, für die externe Sortierfirmen beauftragt werden. Die – durchaus beträchtlichen – Kosten für diese zusätzlichen Maßnahmen werden dem Lieferanten belastet, wenn der fragliche Fehler in seinem Verantwortungsbereich liegt. Deshalb hat er selbst großes Interesse daran, fehlerfreie Komponenten zu liefern.
Treten derlei Fälle öfter auf, stattet der zuständige SQA dem Lieferanten neuerlich einen Besuch ab und überprüft die Verbesserungen, mit denen er gegensteuert. Eventuelle Änderungen im Herstellprozess darf und wird er nicht eigenmächtig durchführen, sondern erst, wenn das auch mit dem SQA des Fertigungsbetriebes abgesprochen und freigegeben wurde.
SCHULUNG ALS HINTERGRUND: DAS SQA CURRICULUM
Die Magna SQA-Mitarbeitenden spielen eine wichtige Rolle bei der Sicherstellung des Qualitätsprozesses beim Lieferanten mit dem Ziel, dass alle produzierten Teile den Anforderungen entsprechen. Sie müssen über die notwendigen Fähigkeiten verfügen, um Probleme zu erkennen und sofort entsprechende Maßnahmen einzuleiten. Deshalb hat Magna frühzeitig damit begonnen, diese Fähigkeiten durch geeignete Aus- und Weiterbildungsprogramme zu entwickeln und auszubauen. Das „SQA Curriculum“ ist eine Art Grundausbildung, die alle Magna SQA Mitarbeitende durchlaufen und besteht aus einem breiten Spektrum an Themen und anwendbaren Inhalten, wie z.B.: Automotive Core Tools, Verständnis von Automotive Standards (VDA, AIAG, IATF, etc.), Ziele und Aufgaben der SQA, Projektmeilensteine und Dokumentationspflichten, Verständnis von Spezifikationen und Toleranzen aus Lieferanten- und Kundensicht, Reklamationsprozess, Verständnis und Anwendung interner Programme und Systeme.
QPF – DIE KOMMUNIKATIONSPLATTFORM ZWISCHEN AUFTRAGSFERTIGER UND LIEFERANTEN
Ebenfalls in Graz gestartet und dann weltweit implementiert hat Magna das eigene Online-Kommunikationssystem. Für die offene und nachvollziehbare Kommunikation mit den Lieferanten hat Magna schon vor über 20 Jahren eine eigene Qualitätsplattform (QPF) geschaffen und seither weiterentwickelt. Dabei handelt es sich um ein Online-Werkzeug, über das die gesamte Kommunikation erfolgt. Das beginnt mit der Auftragsspezifikation bei Projektbeginn und geht weiter mit dem Modul Tool Tracking, das sich auf kritische Werkzeuge bezieht, die zu beschaffen sind und über deren Fortgang der Lieferant regelmäßig berichten muss. Auch die gesamte Dokumentation der Prozessabnahme läuft in dieser Plattform ab, ebenso das Thema Erstbemusterung.
Auch im laufenden Projekt erfasst das QPF-System alle Schritte und Aufgaben, die der Lieferant zu erfüllen hat. Dabei besucht man in regelmäßigen Abständen die Lieferanten und durchleuchtet sie auf ihr Projektmanagement hin. Die Fragen werden im QPF-System gemeinsam ausgefüllt und die Resultate von beiden Parteien festgehalten. Das ergibt dann einen Projektbericht, zeigt eventuelle Schwachpunkte auf und findet ebenfalls wieder Eingang in die Lieferantenbewertung der Qualitätssicherung.
Über die QPF werden auch eventuelle Qualitäts-Claims gemeldet, inklusive Fehlerbeschreibung und Fotos. Die gesamte Abwicklung des Vorgangs fließt in die kontinuierliche Lieferantenbewertung ein. Darüber hinaus ermittelt das System die gesamten Kosten, die durch die Reklamation entstanden sind und dem Lieferanten in Rechnung gestellt bzw. von seinen Rechnungen in Abzug gebracht werden.
NEUE HERAUSFORDERUNGEN IN DER QPF: DIE SOFTWAREENTWICKLUNG
Ein zunehmend wichtigeres Thema ist der Bereich des Software-Engineering. Insbesondere, wenn es um Steuergeräte geht, gibt es bereits sehr gute Vorgaben, die jedoch nur wenige große Lieferanten einhalten können. Kleinere Lieferanten sind oft nicht bereit, ihre Karten offen zu legen. Es wäre möglich, diese abzustrafen, indem man sie auf Stufe "rot" setzt. Dies könnte allerdings dazu führen, dass kaum noch Lieferanten zur Verfügung stehen. Daher ist es erforderlich, alternative Maßnahmen zu ergreifen, um die gewünschten Ziele zu erreichen.
Vor dieser Herausforderung stehen nicht nur Auftragsfertiger in der Automobilproduktion – sondern die Fahrzeughersteller selbst auch. Die Anzahl der heutigen Rückrufe, die auf Softwarefehler zurückzuführen sind, spricht Bände. Insofern birgt das Thema der Software-Qualitätssicherung noch einiges Potenzial für die Zukunft – in der gesamten Branche.
Stay connected with Inside Automotive!
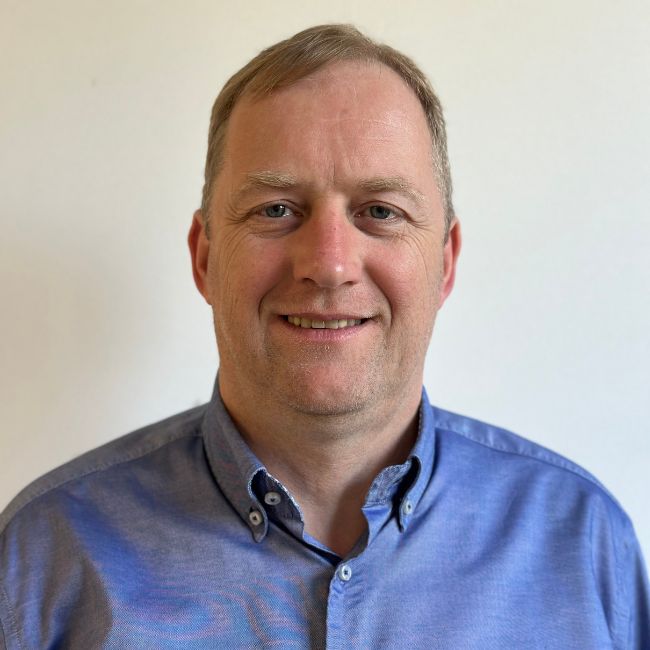
We want to hear from you
Send us your questions, thoughts and inquiries or engage in the conversation on social media.
Verwandte Stories
Verbunden bleiben
Bleiben Sie informiert und erhalten Sie News & Stories in Echtzeit in Ihren Posteingang geliefert.