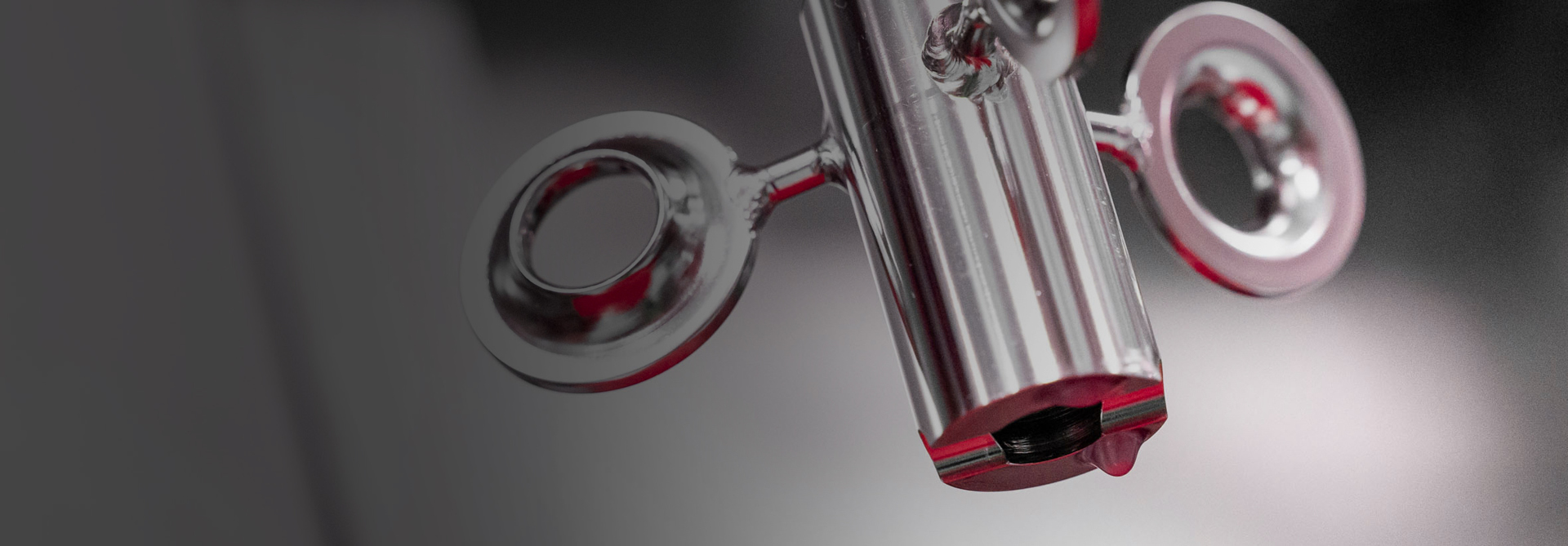
IN THE BEGINNING WAS THE LIMITED EDITION
As a flexible contract manufacturer for the automotive industry, Magna in Graz has always dealt with low-volume and limited edition series. Therefore, an important requirement for the paint shop is the ability to handle small quantities and special coat colors. However, this is a problem for the normal coat painting process used in series production. Attached parts made from plastic, such as bumpers, cannot undergo the baking of the paint coat at the usual 140°C without damage.
For this reason, they usually have to be painted and baked separately from the sheet metal body. In large-scale production, the plastic parts are usually already painted upon delivery. However, this is not practical for low-volume and micro-volume productions, as suppliers are geared towards large quantities.
As a way out of this dilemma, a low-temperature painting process was developed which, like body repair, allows attached plastic parts to pass through the painting process completely intact. This involves lowering the baking temperature from 140°C to around 80°C.
OTHER MATERIALS AND OTHER PROCESSES FOR LOW-TEMPERATURE PAINTING PROCESS
It is not enough to simply lower the temperature in the baking oven. In principle, the low-temperature paint coat application process can be implemented in any existing paint shop. However, other materials must be used. This requires special paints, especially clear coats, which can be baked at temperatures far below the usual 140°C and reach their final strength at this temperature. As far as plastic parts are concerned, special adhesive agents are required to achieve a strong bond between the coating and the component.
Depending on the individual case, the necessary changes can extend into the body shell. Modern joining techniques, in which sheet metal parts – such as aluminum parts – are bonded instead of spot-welded, can be adapted so that the final strength of the bond is achieved in the baking oven. Here too, other materials that do not require high temperatures need to be used.
MODIFIED TECHNOLOGIES AND PROCESSES
Changes to the process, tools and equipment are also required, starting with paint coat application. If plastic parts that are inherently non-conductive are to be coated, electrostatic painting does not work as usual. Different nebulizers are necessary because the usual ESTA fingers, i.e. the electrostatic applicators, may be unsuitable.
Alternatively (or additionally), further measures must be taken to create a conductive surface on plastic parts, by applying conductive primers beforehand or providing exposed pins in conductive “jigs,” for example.
The final step is to change the polishing process. Low-temperature painted parts, namely plastic parts, cannot be treated in the usual polishing process because they are generally more problematic to polish. In many cases, it makes more sense to discard flawed parts and repeat the painting process.
IN ONE FELL SWOOP: PAINTING ATTACHED PARTS TOGETHER WITH THE BODY SHELL
For limited edition series with special paintwork, attached parts that are also to be painted are mounted on appropriate frames and run through the top coat line separately from the body. They are also baked separately in a second baking oven set to a lower temperature. However, the aim is to paint these parts together with the bodywork because this reduces the overall cost – one of the biggest advantages of the low-temperature painting process.
However, the attached parts are not fitted to the body in the same way as during the final assembly. Special auxiliary frames and holders are constructed which are attached to the body and used to fix the attached parts into the installation position. Of course, the work stations required for this must be integrated into the process of moving the body through the paint shop.
Ultimately, painting the attached parts together with the bodywork reduces the amount of work required compared to separate treatment. It also enables efficient and high-quality low-temperature painting process that meets the high and specific requirements of the automotive industry.
THE NEED FOR MODIFIED, IN SOME CASES MORE EXTENSIVE PRE-TREATMENT
For steel and aluminum parts, using the low-temperature process requires essentially the same preparation as the high-temperature process. But the situation is different for plastic parts. Depending on the delivery condition of the attached parts – completely raw and possibly dirty or already primed and base coated – additional work steps are necessary.
To achieve good adhesion, the parts may need to be scarfed and/or wiped before the primer is applied. Depending on the condition, cleaning and degreasing may also be required first. As with the bodywork, perfect preparation is important to achieve a satisfactory paint coating result.
CONTROLS AND INSPECTIONS TO MAINTAIN QUALITY
Every painting process requires careful control of the quality of the coating. In this respect, the low-temperature process is no different from the classic high-temperature method. The resulting surface quality must always meet the high requirements of vehicle painting, but the exact processes can vary depending on customer requirements.
In addition to visual inspections of the finished vehicles, paint thickness measurements, adhesion tests and color adjustments are common. When it comes to the latter, the low-temperature painting process has an advantage. If the body and attached parts are painted together in one single run, the objective color impression (also known as color match) will match more precisely than with separate painting. However, paint thickness measurement on plastic parts must be carried out using a different method than on sheet metal parts, as the conventional method cannot be used on non-conductive plastic.
The various inspection steps must be documented more carefully if attached plastic parts are integrated into the painting process. Plastic parts can rarely be repaired if a defect becomes visible during the coating process, regardless of whether it was already present or occurred during the paint coat application. The corresponding part is then considered a reject and must be replaced with a new one. However, the entire paint coating process must be repeated. Rigorous documentation of the process data is therefore necessary to ensure effective claim management.
PREPARATION AND TRAINING OF PAINT SHOP WORKFORCE
High-quality results and a smooth transition to new processes can only be achieved if the employees in the paint shop are well prepared beforehand. In the case of low-temperature painting processes, the additional work will be minimal as far as the bodywork itself is concerned because the processes fundamentally remain the same. However, the different clear coat finish process for attached parts comes with other requirements since there is a limit to how much heat can be applied when polishing plastic parts.
In the case of attached parts, more training is required depending on the process – particularly regarding cleaning, scarfing, adhesion promotion, and painting efficiency. As a contract manufacturer, Magna has an advantage due to its many years of experience with special series in which a wide variety of attached parts are treated and painted in the factory. This expertise cannot be taken advantage of in the OEMs' own plants, which are primarily designed for high-volume production.
The same applies to the paint shop equipment. Since the low-temperature process has already been in use for some time for these special cases, the paint shop in Graz has two baking ovens: one for conventional 140°C baking, and one for low-temperature baking at 80°C. This is an important USP compared to most other paint shops in the automotive industry.
FASTER OR SLOWER? LOW-TEMPERATURE PAINTING PROCESS AND PRODUCTIVITY
On the one hand, working with the low-temperature painting process increases the added value for the contract manufacturer via the inclusion of attached parts. This can benefit the OEM in the form of a lower overall vehicle manufacturing price. Painting more vehicle parts within cycle times (if attached parts are painted at the same time as the body) generally increases productivity. The better polishability can also increase throughput and at the same time reduce the energy requirement for cooling zones.
On the other hand, the loading process of parts carriers and auxiliary frames can slow down the throughput and require additional space, including the corresponding parts buffers. And depending on the depth of the process, longer drying and baking times may ultimately mean that fewer vehicles can be painted per day.
THE INFLUENCE OF THE LOW-TEMPERATURE PROCESS ON PRODUCT QUALITY
One advantage of painting the body and attached parts together is the extensive elimination of color deviations. This simplifies and shortens the color match or color harmony process and thus reduces integration times. The lower thermal stress also reduces the tensions that arise when using multi-materials – such as the combination of steel and aluminum – due to the different coefficients of thermal expansion. This also contributes to a consistently high quality of the paint coating layer.
Although constant progress is being made in paint development, clear coats that are baked at a lower temperature are not on a par with those baked at 140°C in terms of chemical and mechanical durability. Particularly because they do not yet reach their high level of scratch resistance. In addition, more precise process controls are required because the process windows for cross-linking and baking are narrower.
However, the benefits and necessity of the extremely high resistance of today's high-temperature clear coats may also be challenged. A lower scratch resistance of attached parts can already be observed today in vehicles whose bodywork has been painted using a high-temperature process, but the plastic parts are inevitably painted at lower temperatures – usually at the supplier in large-scale production.
As a result, bumpers, skirts and other plastic elements “age” quicker and the different surfaces visually diverge after a longer period of use. If everything is painted together in a low-temperature painting process, the attached parts and body “age” together, so to speak.
Of course, it is difficult to make predictions. But it can be expected that the requirements of many car manufacturers and OEMs - especially the German premium brands - will return to a more realistic level in the medium term as far as the resistance of body surfaces is concerned. Some manufacturers have already started to treat parts of the outer skin using the low-temperature process, such as contrast-painted vehicle roofs. In addition, the low-temperature painting process has already been industrialized in the commercial vehicle sector and for some low-volume sports cars.
WILL THE FUTURE BELONG TO THE LOW-TEMPERATURE PAINTING PROCESS?
The key advantage of the low-temperature painting process is the overall lower energy requirement and therefore progress in the decarbonization of automotive production. This aspect is becoming increasingly important. Naturally, this is also accompanied by a reduction in energy costs. This is why virtually all car manufacturers and OEMs are working on lowering temperatures throughout the entire coating and painting process to reduce energy consumption and the CO2 footprint of production.
This is partly due to cost pressure. However, it also helps fulfill legal requirements and specifications for sustainable production. Because the paint shop is the most energy-demanding part of the entire car production process, low-temperature painting is a “low-hanging fruit” compared to other efforts to reduce CO2 emissions in automotive production since it can achieve very large improvements.
This not only applies to the top coat, but also includes previous steps, such as cathodic dip coating. Future developments can further promote the low-temperature painting process for the top coat. In order to accommodate additional sensors for Level 3 and 4 automated driving, for example, it is advisable to manufacture larger parts of the outer body shell from plastic. Here, low-temperature painting creates greater scope and more freedom in product design through the use of composite materials. It also allows a greater variety of materials to be used in lightweight construction.
The general trend towards shorter model cycles, and therefore lower overall quantities, may further increase the importance of the low-temperature painting process, especially since there is an increasing demand for individualization and special colors, particularly in the high-price segment. It makes it easier to produce low-volume and limited series. There are many indications that low-temperature painting will play an important role in the automotive industry in the future, as it combines ecological and economic benefits.
Stay connected with Inside Automotive!

We want to hear from you
Send us your questions, thoughts and inquiries or engage in the conversation on social media.
Related Stories
Stay connected
You can stay connected with Magna News and Stories through email alerts sent to your inbox in real time.