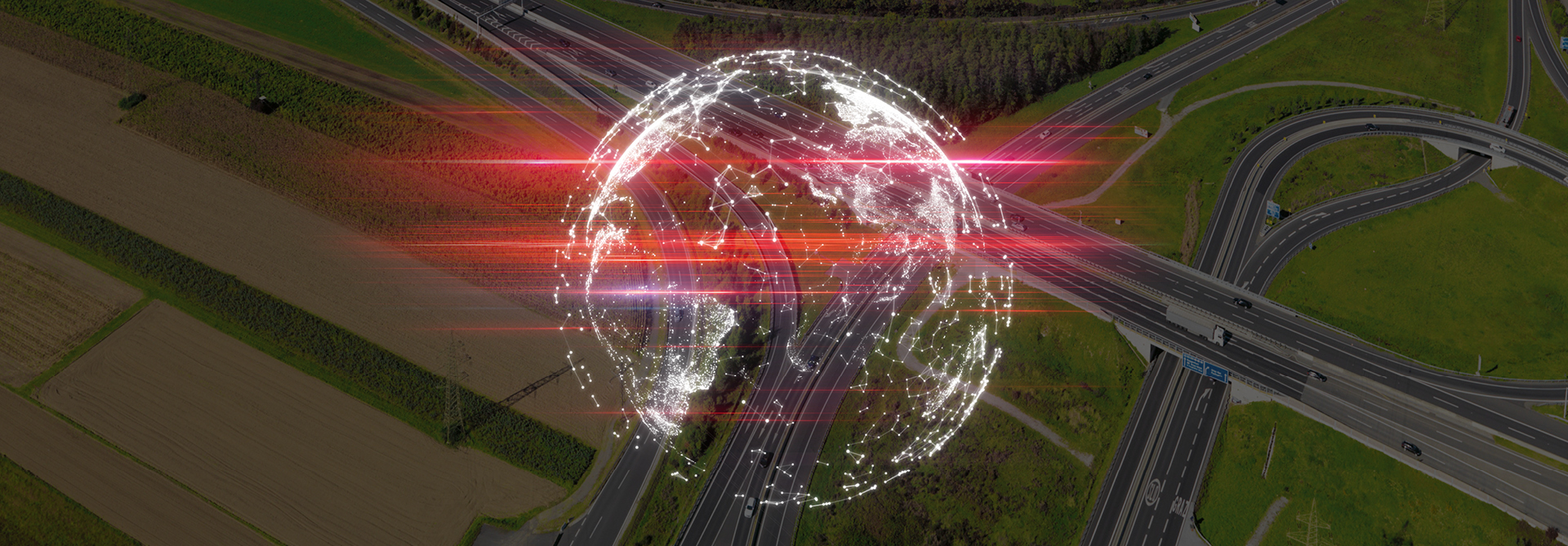
DECARBONIZED VEHICLE PRODUCTION THROUGH SUSTAINABLE LOGISTICS
The carbon footprint of a product or individual is organized into different phases, also known as scopes. In relation to vehicle production, Scope 1 refers to the direct CO2 emissions during the production of the vehicle. This emission is generated by energy consumption during the manufacturing process. Scope 2 relates to the production of energy. Scope 3 considers the energy consumption both before and after the actual production of the product. This includes energy consumption in the procurement and manufacture of raw materials and components, as well as the transportation of parts and of the end product. Indirect expenditures inside and outside the plant are also taken into account.
AVOIDING CO2 EMISSIONS AND REDUCING UNAVOIDABLE EMISSIONS
In sustainable logistics, the ideal transportation is one that does not take place after all. To reduce the number of transports, it is possible to optimize the transport network. One possibility is to increase the capacity of the necessary transports to reduce their number. This can be achieved by placing orders in advance to achieve a higher utilization of the transports. In addition to the optimization of pick-up frequencies and an efficient choice of transport type, such as the creation of milk runs, further improvements can be realized.
The key term here is: transport-optimized delivery schedule. The potential for saving transports is enormous. The next step is to switch unavoidable transportation to low-CO2 or CO2-free means of transport. Combined road-railroad freight transport can make a decisive contribution to this.
COMPREHENSIVE OPTIMIZATION OF THE MATERIAL FLOW THROUGH iTMS
To determine and evaluate the total CO2 value, a certified calculation model is used. Magna employs a module of its own integrated transportation management system (iTMS). All relevant consignment data and other parameters required to evaluate the CO2 value of any transport are available here: size and weight of the goods to be transported, transport types, distances, etc. The CO2 emissions caused by the transport can be calculated and evaluated from this data.
This backbone can also be utilized to identify opportunities to improve the efficiency of transport logistics. This is because the iTMS manages the entire material flow of automotive production - from ordering materials from suppliers to the plant to delivering returnable load carriers back to the suppliers.
SUSTAINABLE LOGISTICS STARTS WITH THE SELECTION OF SUPPLIERS
In automotive production, logistics planning starts as early as the development process of a product. Every sourcing decision also involves taking the necessary transportation into account and recording its significance both in monetary terms and in terms of the associated CO2 emissions. The decision is then made based on an analysis of the total cost of ownership (TCO).
The aspect of transport efficiency in Simultaneous Engineering can also influence the design of the components to be delivered. For example, bulky parts or modules that entail the transportation of a lot of air could be shipped partially disassembled rather than pre-assembled. This increases the overall packing density. Ultimately, it is always a question of weighting options and overall assessment.
THE IMPACT OF PACKING AND PACKAGING CONCEPTS IN SUSTAINABLE LOGISTICS
These measures - which of course always require close cooperation with the suppliers - cannot always achieve optimum packing density to minimize the number of transports. However, transport space can be used more efficiently by nesting several units of a bulky component together. This is where the development of a suitable packaging design is essential to reduce the packing volume and thus the transport-related CO2 emissions.
CLOSE COOPERATION WITH SUPPLIERS IS A MUST
Close cooperation with suppliers is essential in the planning and execution of processes. In the vast majority of cases, they are very willing to do so because the usefulness and advantages of an integrated transportation management system are relatively easy to convey.
Of course, the prerequisite remains that the manufacturing company communicates openly with its suppliers through these systems. For example, among the 1,700 or so pick-up points from which Magna procures components for series production at its Graz plant, there are only a handful of “deniers” that do not (yet) want to be connected to the overarching systems.
SHOULD LOAD CARRIERS BE REUSED OR RECYCLED?
As part of sustainable logistics, efforts are generally made to use reusable load carriers – where possible, standard load carriers that can be utilized for different components and many suppliers, like the VDA's KLT boxes, steel load carriers or large plastic containers, depending on which components are to be transported. Special load carriers that are specifically designed for the geometry of the component are also used depending on their requirements. This is common practice, at least among European automotive suppliers.
However, deliveries from overseas can be different. This is because the return transportation of reusable load carriers requires high financial and energy costs, which defeats the point of the whole operation from an ecological point of view. In these cases, it is more advisable to use single-use load carriers and disposable packaging. These load carriers and packaging are then designed to be either as materially homogeneous as possible, or can be dismantled so that they can be recycled as easily as possible.
INTERMODAL TRANSPORTATION CAN HELP REDUCE EMISSIONS
For sustainability reasons, rail transport is generally preferable to road transport because electrified trains are locally emission-free. In this respect, the road-railroad combination offers an attractive solution for reducing overall emissions. However, this only applies to situations where an existing logistics product can be used. In such cases, transit times are often only marginally longer than for pure road transportation, and the connection can be reliably planned.
This can be seen in transports from the Ruhr region to Graz, where there is an efficient connection from the freight terminal near Neuss to the cargo terminal in Graz. The situation is similar for transports from England, where there is an efficient connection from the ferry port of Rotterdam.
OPPORTUNITIES AND POSSIBILITIES OFFERED BY TRUCKS WITH ALTERNATIVE DRIVE SYSTEMS
Alternative drive systems offer an intriguing opportunity for sustainable logistics to reduce CO2 emissions from truck transportation. At least for relatively short distances, battery electric vehicles are currently a viable option, even if they initially require considerable investments, especially for the charging infrastructure, so that the charging process can be integrated directly into the process.
For rail connections from the terminal to the plant or for linking external logistics warehouses with the plant, this option is feasible. To connect to an external body store, Magna has already been using an electrically powered truck whose drive batteries are recharged during loading and unloading for several years. This system is also already in use for shuttle services to an external warehouse.
Hydrogen propulsion is also a possibility for long-distance trucks, but not in the near future. The vehicles are hardly available yet, and the public refueling infrastructure is still lacking, like the high-performance charging infrastructure for long-distance trucks with battery-electric drives.
Alternative fuels can also be appealing as a bridging technology on the way to zero-emission transportation in automotive production. Hydrogenated vegetable oils (HVO) are especially promising as a fuel for existing diesel trucks and can bring an immediate CO2 reduction in the range of 80 to 90 percent. Admittedly, this option is also limited due to the availability of the raw material, and it does not result in a completely CO2-free transportation. However, this technology can be implemented quickly with very little effort and virtually no infrastructure costs.
With bio-LNG, the required effort is greater because special LNG-compatible trucks are needed, or the existing vehicles have to be converted at a high cost. Ultimately, there is no perfect patent solution, but a combination of different approaches promises the most advantages.
CHALLENGES IN THE IMPLEMENTATION OF SUSTAINABLE LOGISTICS
Increasing complexity is a major challenge in the efforts to reorganize logistics in the automotive industry in an ecologically sustainable way. The required mix of different concepts for different tasks brings with it even greater complexity. Also, an assessment is needed as to which technologies will ultimately prevail, depending on which are favored by politicians and for which the infrastructural conditions are created or improved.
Occasionally, political changes such as Brexit also create new challenges to be solved. And of course, any efforts to achieve sustainable logistics can only be truly successful if the employees are also on board. It is an important task for Magna as a contract manufacturer in automotive production to inspire employees, particularly new employees, to adopt this mindset and get them on board.
FUTURE TRENDS IN LOGISTICS AND THEIR OPPORTUNITIES FOR GREATER SUSTAINABILITY
Digitalization will continue to increase in sustainable logistics – and not just to overcome the challenges posed by increasing complexity. Further integration of the data flow, including across company boundaries, will be necessary to achieve better cooperation and greater logistics security.
Catena X is a buzzword that is currently gaining momentum in the German automotive industry. It is a new IT technology that enables the individual proprietary systems of different companies to be linked together to increase transparency. This makes it possible to optimize supply chains, plan logistics more efficiently and eliminate transports altogether where possible. Because every transport that does not take place reduces CO2 emissions and is therefore a further step towards sustainable automobile production.
Stay connected with Inside Automotive!
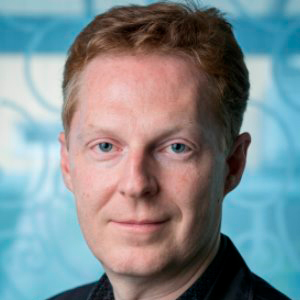
We want to hear from you
Send us your questions, thoughts and inquiries or engage in the conversation on social media.
Related Stories
Test First, Then Enter the European Market: Professional Battery Testing Examines More Than Just the Charging Curve
Blog
Quality Assurance at a Contract Manufacturer for Serial Production in the Automotive Industry
Blog
Stay connected
You can stay connected with Magna News and Stories through email alerts sent to your inbox in real time.