
Spezial-Know-How und Geo Skid – So sorgt ein Multi-OEM-Auftragsfertiger
für höchste Qualität und Flexibilität
- Erwin Fandl
- Januar 08, 2024
- 5-min read
Die Automobilindustrie ist im Umbruch; nicht nur die Umstellung auf alternative Antriebe, sondern auch die immer weiter differenzierten Endkundenerwartungen erfordern eher kleinere Stückzahlen pro Automodell. Wie lässt sich die Produktion auch kleiner Serien auf einer Großserienanlage kosteneffizient und hochqualitativ darstellen?
HOHE FLEXIBILITÄT AN DER LINIE BEI EINEM MULTI-OEM-FERTIGER
Der Schlüssel liegt darin, mehrere kleinere Serien auf einer gemeinsamen Großserienanlage herzustellen. Dafür ist es notwendig, einen hohen Grad an Flexibilität in der Anlage zu haben. Es muss möglich sein, innerhalb der Fertigungszeit bzw. der Förderzeit von Takt zu Takt oder von Fertigungsschritt zu Fertigungsschritt auf ein anderes Modell umzurüsten.
Im Rohbau stellt sich weniger das Problem des Box-Maßes, also der Karosserieabmessungen und Volumina, im Gegensatz zur Lackiererei – zumindest im Pkw-Bau. Stattdessen besteht hier die Aufgabe, eine zuverlässige Aufnahme der Karosseriebasis bereitzustellen, die an jeden der auf der Anlage gefertigten Fahrzeugtypen angepasst werden muss.
ADAPTIERUNG DER AUFNAHMEPUNKTE DURCH SPEZIELLEN TRANSPORTSCHLITTEN
Sollen mehrere unterschiedliche Fahrzeugtypen auf der gleichen Rohbau-Linie laufen, besteht die wichtigste Herausforderung in den unterschiedlichen Aufnahmepunkte des Unterbodens. Diese werden nicht vom Auftragsfertiger festgelegt, sondern sie sind durch die Fahrzeugarchitektur vorgegeben.
Dabei gibt es auch unterschiedliche Konzepte, wie aufgenommen wird: Schrauben, Stecken und Verriegeln – die Hersteller verfolgen unterschiedliche Ansätze. Ein Multi-OEM-Fertiger muss mit allen unterschiedlichen Aufnahmekonzepten umgehen können. Das in OEM-eigenen Großserienanlagen übliche Konzept der modellspezifischen Aufnahmevorrichtungen, oft umgesetzt als Bodenspannvorrichtung, ist also nicht umsetzbar, wenn der Karosseriebau unterschiedliche Modelle herstellen soll.
Dazu wurde bei Magna eine besondere Art eines modularen, flexibel adaptierbaren Aufnahmesystems entwickelt – der flexible Geo Skid.
Entwickelt wurde er aus dem bei Magna schon seit über 20 Jahren eingesetzten, Geo Skid genannten Fertigungsschlitten. Dieser entstand aus dem Bestreben, die Fertigungspräzision zu erhöhen. Dabei wird auf die Verwendung von Unterbodenspannsystemen verzichtet, um die Karosserie in den unterschiedlichen Stationen jeweils wieder neu zu zentrieren, denn jeder erneute Aufspannvorgang kann potenziell Ungenauigkeiten erzeugen. Stattdessen wird der Unterboden am Anfang des Rohbaus im Geo Skid fixiert, und der Skid wird in der jeweiligen Station festgesetzt.
DER MODELLSPEZIFISCH ADAPTIERBARE GEO SKID ALS VORAUSSETZUNG FÜR FREIEN MODEL-MIX AUF DER KAROSSERIEBAULINE
Unterschiedliche Karosserievarianten auf einer Linie zu fahren – etwa Limousine, Kombi, Schrägheck oder auch SUV – wird heute auch im Hersteller-eigenen Karosseriebau umgesetzt. Dabei wird aber immer auf einem einheitlichen Unterboden aufgebaut. Die Herausforderung bei einer Multi-OEM-Fertigung besteht primär darin, mit unterschiedlichen Unterböden umzugehen. Es werden also Fahrzeuge auf einer Linie gebaut, die grundlegend nichts miteinander zu tun haben müssen – weder von der Fahrzeug-Grundarchitektur, noch von den Aufnahmepunkten her.
Daher ist hier ein Aufnahmesystem erforderlich, dass alle auf der jeweiligen Linie produzierten Karosserien beherrscht. Der patentierte flexible Geo Skid von Magna besteht prinzipiell aus einem einheitlichen Grundrahmen, an den die modellspezifischen Aufnahmen mit Nullpunkt-Spannsystemen spielfrei montiert werden und schon von daher die geometrische Präzision sicherstellen. Anders als bei den nur in einer Richtung variierbaren Schlitten, wie sie auch in einigen Werken der Hersteller für unterschiedliche Modellderivate eingesetzt werden, sind beim flexiblem Geo Skid alle Aufnahmepunkte verstellbar und können dem jeweiligen Produkt angepasst werden.
Magna ist mit diesem seit 2022 eingesetzten Konzept Vorreiter in der Automobilindustrie und insofern einzigartig – auch wenn namhafte OEM bereits an ähnlichen Konzepten arbeiten, um in neuen Werken beispielsweise auf einer Linie die Fertigung von unterschiedlichen Fahrzeugen mit unterschiedlichen Antriebskonzepten zu integrieren.
UMFASSENDE AUTOMATISIERUNG ALS VORAUSSETZUNG FÜR FLEXIBLEN KAROSSERIEROHBAU
Für jeden gefertigten Fahrzeugtyp ist auf der Linie – abhängig von den zu fertigenden Stückzahlen – eine bestimmte Menge an fertig adaptierten Geo Skids im Umlauf. Das ist nur durch umfassend integrierte virtuellen Planungssystemen und Simulationen möglich, allein schon, um den Rückfluss der Skids von Ende der Linie zurück zum Anfang sicherzustellen. Mit manuellen Konzepten wäre ein solch komplexer Fertigungsprozess gar nicht darstellbar.
Deshalb ist es erforderlich, dass jeder Fertigungsschritt in die Automatisierung eingebunden werden kann – von der Heranführung der jeweils benötigten Blechteile an die Linie über die Werkzeugwechselsysteme bis hin zur jeweiligen Füge- und Verbindungstechnologie: Punktschweißen, Kleben, Nieten oder auch Laserprozesse. Einzelne Skids können dabei aus dem Fertigungsprozess genommen und wieder eingeschleust werden – etwa, um die Skids umzurüsten und sie damit einem geänderten Modell-Mix anzupassen; oder auch, um Wartungsarbeiten ohne Unterbrechung der Fertigung durchzuführen.
INDIREKTE TOLERANZÜBERWACHUNG FÜR HÖCHSTE FERTIGUNGSPRÄZISION UND UNTERBRECHUNGSFREIE PRODUKTION
Einen besonderen Stellenwert für die Herstellung hochqualitativer Endprodukte hat die präzise Einhaltung von Fertigungstoleranzen bereits im Karosserierohbau. Dabei hat Magna ein besonders smartes System zur fortlaufenden Überwachung der Fertigungspräzision entwickelt: Während des Produktionsprozesses sind die Fertigungsschlitten mit ihren Aufnahmevorrichtungen nicht zugänglich und können daher nicht vermessen und kontrolliert werden. Sie mussten daher traditionell in regelmäßigem Turnus aus dem Prozess genommen, im Messraum inspiziert und nötigenfalls gewartet werden: ein zeitraubender und kostenintensiver Vorgang.
Magna’s Indirect Automated Body-In-White Fixture Controller spart dies und sorgt darüber hinaus für noch höhere Fertigungspräzision: Anstatt die Aufnahmerahmen selbst in festgelegten Intervallen aus der Linie zu nehmen und zu kontrollieren, werden im laufenden Produktionsprozess die produzierten Rohkarosserien mit Hilfe des intelligenten Systems genauestens vermessen.
So lassen sich schon Tendenzen zu Abweichungen der geometrischen Maßhaltigkeit vorausschauend erkennen, noch ehe sie zu ernsthaften Ungenauigkeiten führen. Jede Abweichungstendenz lässt sich auf den jeweiligen Geo Skid zurückverfolgen; so kann genau dieser Skid ausgeschleust, gewartet und rekalibriert werden.
Auf diese Weise werden die Aufnahmeschlitten nicht nur in festgelegten Intervallen, sondern faktisch kontinuierlich überwacht. Das zahlt sich nicht nur in Form einer konstant hohen Fertigungspräzision aus, die insbesondere für Endprodukte im Premium-Segment gefordert ist, wie sie bei Magna gefertigt werden. Gleichzeitig wird der Zeit- und Kostenaufwand im Prüfprozess reduziert und die eventuelle Notwendigkeit von Nacharbeit vermieden.
RÄUMLICHE NÄHE ALLER FUNKTIONEN FÜR DIE FERTIGUNGSANLAGEN ERLAUBT SCHNELLE INTEGRATION NEUER PRODUKTLINIEN
Eine besonders Stärke der Fertigung bei Magna ist die Konzentration von Planung, Entwicklung, Instandhaltung und Produktion an einem Standort. Die sehr straffe Organisation und die nicht nur räumlich, sondern auch organisatorisch kurzen Wege sorgen für verlustarme Kommunikation und ermöglichen die schnelle und flexible Umsetzung. Seit 1. Januar 2024 heißt dabei das Konzept: Anlage als Service. Somit kommen Planung und Instandhaltung unter einen Hut, also in einen Entwicklungsprozess. Das Ganze steht unter dem Stichwort „Nähe zur Produktion.“
Die kurzen Organisationswege vereinfachen auch die Integration neuer Produkte in die Fertigung. Gerade in der gegenwärtigen Umbruchsituation in der Automobilindustrie ist die Verkürzung der „Time to Market“, also die Schnelligkeit, mit der ein neues Produkt auf den Markt gebracht werden kann, ein entscheidender Erfolgsfaktor für den OEM.
SKALIERBAR UND BALANCIERBAR: DIE VORZÜGE EINER FLEXIBLEN MULTI-OEM-AUFTRAGSFERTIGUNG
Ein flexibler Fertigungsprozess hat daneben auch den Vorzug, während der Laufzeit eines Fahrzeugmodells flexibler auf veränderte Stückzahlerfordernisse etwa durch Nachfrageveränderungen reagieren zu können. Prinzipiell ist, technisch gesehen, die Fertigung ab der Loszahl Eins möglich – auch wenn bei sehr geringen Stückzahlen natürlich keine finanziell vertretbare Produktion möglich sein wird. Nach oben wird die realisierbare Stückzahl nur durch die technische Auslegung der Anlage limitiert – dargestellt in Einheiten pro Stunde – und durch die Anzahl der Produktionsschichten.
Bei Magna wird der Karosseriebau im Dreischichtbetrieb ausgelegt; das hat für den Hersteller den Vorteil geringerer erforderlicher Investitionen, als wenn nur in zwei Schichten produziert wird. Bei einem Zweischichtmodell müsste für den gleichen Fahrzeugoutput die Linie länger sein, was mit größeren Investitionen einhergeht. Bei Markt- oder Nachfrageänderung kann bereits im Karosseriebau, wie auch in den nachfolgenden Produktionseinheiten, relativ kurzfristig zwischen den einzelnen Produkten balanciert werden. Dabei muss der Rohbau nicht exakt entsprechend der Fertigungssequenz an der Montagelinie gefahren werden, sondern kann ein Stück weit entkoppelt laufen; denn die Rohkarosserien werden ja ohnehin vor der Lackiererei und vor der Montage gepuffert.
Dennoch ist die flexible Anpassbarkeit bereits im Karosserie-Rohbau ein essenzieller Baustein der flexiblen Auftragsfertigung; und die kann die Antwort auf die Herausforderungen sein, die sich dem Hersteller aufgrund zunehmend größerer Variantenzahl und kürzerer Modelllaufzeiten stellen.
Stay connected with Inside Automotive!
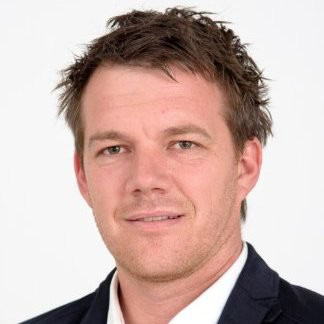
Christian Knollmayr
Christian Knollmayr ist bei Magna in Graz für das Center of Compentence Body in White verantwortlich, welches alle Planungsdisziplinen rund um den Karosseriebau umfasst; seit Jahresanfang 2024 hat er auch die Position des AGM der Business Unit Painted Body inne. Nach seiner Ausbildung, HTL für Maschinenbau und Automatisierungstechnik trat er 2000 in das Unternehmen ein und war seither unter anderem in den Bereichen CoC Lackiererei und FD Qualitätswesen tätig.
We want to hear from you
Send us your questions, thoughts and inquiries or engage in the conversation on social media.
Verwandte Stories
Verbunden bleiben
Bleiben Sie informiert und erhalten Sie News & Stories in Echtzeit in Ihren Posteingang geliefert.