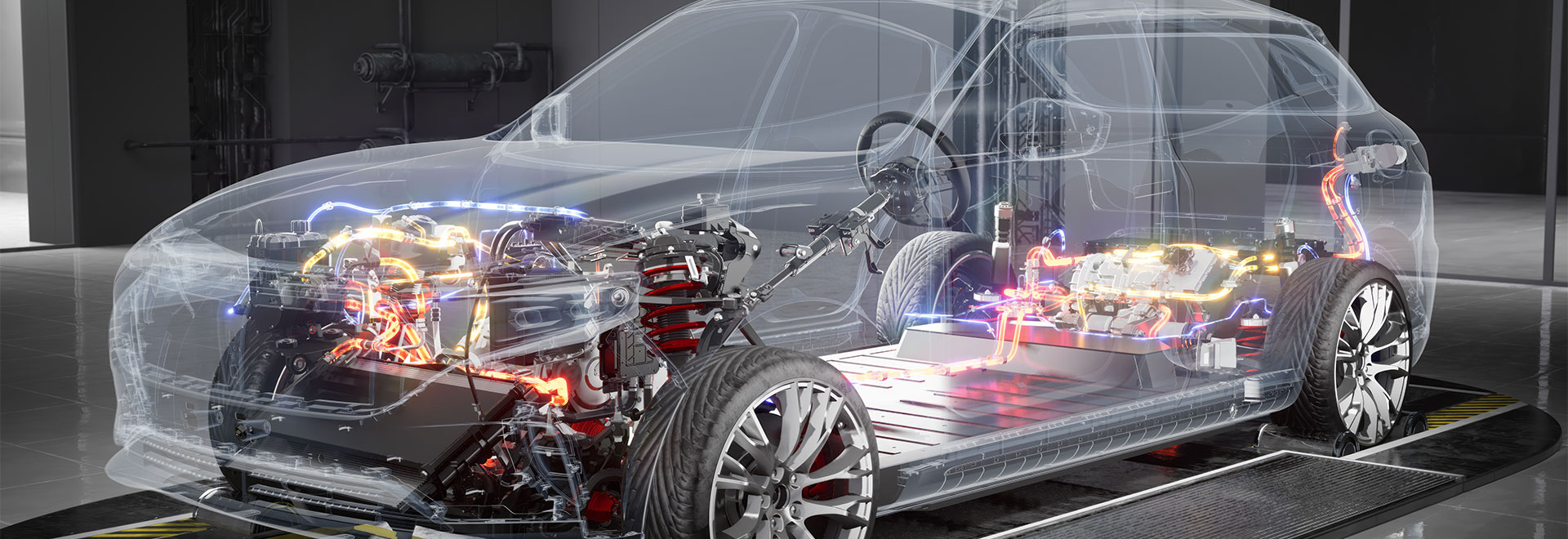
In Zukunft über 1000 Volt? Integration von HV-Batterie und Antriebsstrang ins E-Auto
- Gerald Gartler
- Dezember 11, 2023
- 3-min read
400 Volt, 800 Volt, 915 Volt: Die Spannungslage in E-Autos scheint nur eine Richtung zu kennen – nämlich nach oben. Gelegentlich ist deshalb die Meinung zu hören oder zu lesen, dass wir in Zukunft alle mit über 1000 Volt fahren werden. Doch ist eine höhere Spannungslage wirklich in allen Fällen die beste Wahl – oder hat die Umstellung weg von 400 Volt, die sich bislang als Standard-Spannungslage etabliert haben, auch Nachteile?
Die Vorteile einer höheren Spannungslage sind zunächst überzeugend: Weil sich bei höherer Spannung mehr Leistung bereitstellen lässt, ergibt sich die Möglichkeit höherer Ladegeschwindigkeiten. Und weil es dabei möglich ist, die Kabelquerschnitte zu reduzieren, kann eine höhere Spannungslage auch dabei helfen, das Gewicht des E-Autos zu senken – was sich positiv auf Beschleunigung und Reichweite auswirkt.
KÜRZERE E-AUTO-LADEZEITEN EI LIMITIERTEM LADESTROM
Ein Grund dafür, dass der Trend zu höherer Spannungslage vor allem in großen, leistungsstarken E-Autos anhält, liegt in der Limitierung der Ladeströme. Es gibt hier gesetzliche Beschränkungen: Wenn sehr große HV-Batterien in kurzer Zeit geladen werden sollen, führt der Weg nur über ein Anheben der Spannung: Weil sich die Ladeleistung aus dem Produkt von Ladespannung und Ladestrom ergibt (P=U•I), steigt bei gleichem Ladestrom die Leistung, wenn die Spannung angehoben wird.
Dadurch erhöht sich die Ladegeschwindigkeit, während sich die benötigte Ladezeit für die HV-Batterie signifikant reduziert: Bei einem typischen Nachladevorgang ist eine Verkürzung der Zeit auf weniger als 50 % erzielbar. Das trägt entscheidend dazu bei, auf längeren Strecken, die einen Ladestopp erfordern, die Gesamtreisezeit zu verkürzen. Das E-Auto kann damit im Idealfall vergleichbare Gesamt-Reisegeschwindigkeiten erzielen wie ein konventioneller Verbrenner – oder sich diesen zumindest annähern.
Allerdings sind der Optimierung hier Grenzen gesetzt: Über eine höhere Spannungslage eine signifikant höhere Ladegeschwindigkeit zu erzielen, funktioniert nur zu einem bestimmten Grad. Denn bei den einzelnen Zellen der HV-Batterie gibt es ein physikalisches Limit, wie viel Strom diese maximal aufnehmen können – unabhängig von der Spannungslage der HV-Batterie. Wird dieses Limit erreicht, erhält man durch eine weitere Erhöhung der Spannung nur eine geringfügig höhere Ladegeschwindigkeit. Insofern wird die Entwicklung hin zu immer höheren Spannungslagen an eine Grenze stoßen, die zum einen wegen der Zellen zustande kommt und zum anderen durch die Ladeinfrastruktur beschränkt ist.
HÖHERE SPANNUNGSLAGE KANN GEWICHT SPAREN UND EINPASSUNG IN DEN FAHRZEUGVERBUND DES E-AUTOS ERLEICHTERN
Um die gleiche elektrische Leistung bereitzustellen, reichen bei höherer Spannungslage geringere Stromstärken. Dafür genügen wiederum Leiter mit geringerem Querschnitt, weil die Verlustleistung erheblich reduziert wird. Zum Beispiel ergibt sich bei einer Ladeleistung von 200 kW bei der branchenüblichen Spannungslage von 400 V eine Verlustleistung von 85 W pro Meter Leitung, wenn Anschlussleitungen von 50 mm2 verwendet werden. Betrachtet man diese Verlustleistung als akzeptabel, genügt bei 800 V Spannung ein Fahrzeug-Kabelquerschnitt von nur 12,5 mm2, bei 1000 V reichen sogar Querschnitte von nur 8 mm2.
Damit lässt sich nicht nur das Gewicht erheblich reduzieren und damit Fahrdynamik, Performance und Reichweite verbessern; die Leitungen werden auch flexibler und lassen sich besser im Fahrzeug unterbringen und verlegen. Die Isolierungsanforderungen von 400 V bis 1000 V ändern sich dabei nicht; bereits jetzt wird für 400 V die doppelte Isolierung für die Hochhvoltverkabelung im Fahrzeug verwendet, was auch für höhere Spannungen ausreichend ist.Leiterquerschnitte für unterschiedliche Spannungslagen bei gleicher Verlustleistung: Bei höherer Spannung wird signifikant weniger Leiterquerschnitt benötigt
Das Sparpotenzial beim Gewicht ist beträchtlich: Wiegt eine Leitung für 150 kW Leistung bei 400 V Spannung 1,27 kg pro Meter, reduziert sich das Gewicht des leitenden Kupfers bei 800 V auf nur 673 g pro Meter, also kaum mehr als die Hälfte. Der für die gleiche Leistung benötigte niedrigere Stromfluss machen sich aber nicht nur bei den Lade- und Versorgungsleitungen positiv bemerkbar: Durch den geringeren Leiterquerschnitt lassen sich auch die Wicklungen in den Motoren kompakter auslegen, wodurch die Baugröße der Motoren reduziert werden kann. So hat sich nach Angaben eines deutschen OEMs das Fahrzeug-Gesamtgewicht durch die Verdopplung der Spannung in Summe reduziert. Im gleichen Maß sinken natürlich auch die Materialkosten
KOSTENSTEIGERUNG DURCH HÖHERE SPANNUNGSLAGE
Andererseits verursacht die höhere Spannungslage andernorts höhere Kosten. Zum einen liegt das an der Tatsache, dass viele Komponenten durch die Dominanz der 400-Volt-Architektur in größeren Stückzahlen und von mehr Herstellern geliefert werden als entsprechende Komponenten für die 800-Volt-Technik. Deshalb sind sie einfach preiswerter verfügbar. Zum anderen müssen – zumindest in der Einführungsphase der 800-Volt-Architektur – einige Systeme im Fahrzeug doppelt ausgeführt werden: Die Ladeinfrastruktur ist derzeit noch auf 400-Volt-Fahrzeuge ausgelegt und es gibt kaum Ladesäulen, die schon mit 800 V laden können. Deshalb kann im Fahrzeug ein weiterer DC/DC-Wandler erforderlich sein, der die 400 V aus der Ladesäule auf die 800 V im Fahrzeug umsetzt.
Ein weiterer Kostenfaktor ist, dass bei 800 V höhere Anforderungen an bestimmte Geräte gestellt werden. So muss der Inverter vor dem Motor höhere Spannungen schalten können; und auch das Wandeln auf niedrige Spannungen beim Start-Up (900 V auf 30-40 V) ist komplexer. Dies ist notwendig, um die Funktion aller elektrischen Geräte vor dem Starten zu überprüfen.
LÄNGERE ENTLADEZEIT DES E-AUTOS BEI HÖHERER SPANNUNGSLAGE
Durch die höhere Spannungslage wird in den Zwischensystemen, etwa den Leitungen innerhalb des Fahrzeugs, erheblich mehr Energie gespeichert: Die Energiemenge wächst im Quadrat zur Spannung. Zum Beispiel verbleiben in einem System, in dem bei 400 V eine Energiemenge von 120 J verbleibt, bei 800 V schon 480 J, bei 1000 Volt gar 750 J. Das stellt eine Herausforderung für das geforderte Schnellentladen aller Fahrzeugsysteme dar.
Dabei ist gefordert, dass spätestens 5 Sekunden nach dem Notabschalten des Fahrzeugs, etwa nach einem Crash, alle Teile potenzialfrei sind – bzw. zumindest kein höheres Potenzial als 60 V anliegen darf. Zum Abbau des Restpotenzials genügt bei der „klassischen“ 400-Volt-Spannungslage in der Regel eine einzige aktive Entladeeinheit als Electric Discharge Unit (z.B. elektrische Antriebseinheit).
Bei höherer Spannungslage ist die Restenergie in den Zwischensystemen aber so groß, dass aktive Entladung an mehreren Stellen erforderlich ist, um die geforderte rasche Entladung aller Komponenten herbeizuführen. Der Trend geht dabei dahin, dass jede Komponente sich selbst entlädt. Das ist technisch durchaus lösbar, treibt aber die Kosten nach oben. Ebenfalls kostentreibend wirkt sich das komplexere Batteriemanagement-System (BMS) aus. Dieses ist bei höherer Spannungslage erforderlich, weil mehr Zellen in Reihe hintereinander geschaltet werden müssen.
TECHNISCHE HERAUSFORDERUNGEN DURCH ERHÖHTE SPANNUNGSLAGE
Auch im Bereich der Inverter für die Motorregelung ist ein erhöhter Aufwand bei höherer Spannungslage erforderlich. Die darin verwendeten elektronischen Schaltelemente (konventionell sind das Silizium-IGBTs) können bei den auftretenden Spannungsspitzen an ihre Grenzen geraten. Damit ist der Wechsel zu einem anderen Material – etwa Siliziumkarbid (SiC) – erforderlich, um die geforderte hohe Schaltleistung sicherzustellen.
Die Schaltverluste hängen hierbei linear von Spannung, Strom, Schaltdauer und Schaltfrequenz ab. Bei gleichbleibender Leistung, höherer Spannung und niedrigerem Strom kann die Verlustleistung durch das Verwenden schnell schaltender SiC-IGBTs abgemildert werden.
Bei genauer Untersuchung kann auch ein teurer Wechsel der Inverter-Architektur diese Herausforderungen lösen. Auch hier ist in Abstimmung mit dem OEM abzuwägen, ob die bessere Effizienz die höheren Kosten aufwiegt.
Bestehen bleibt die Erhöhung der elektromagnetischen Interferenz (EMI), also das Entstehen von Störungen innerhalb des Inverters. Verbesserte Filtereinheiten am Ausgang des Inverters verhindern das Ausbreiten der EMI entlang der Kabel und Leitungen. Ein geschirmtes HV-Bordnetz verhindert das Übergreifen von EMI an umgebende Baugruppen.
EMI können zum einen zu Störungen an elektronischen Baugruppen im Fahrzeug führen, zum anderen aber auch Schäden an der Isolation der Motorwicklungen verursachen, was die Motorlebensdauer verkürzt.
Höhere Spannungslage löst nicht alle Probleme von E-Autos
Wie sich zeigt, ist der Wechsel auf eine höhere Spannungslage als die derzeit branchenüblichen 400 V keineswegs eine Patentlösung, um Effizienz, Performance und Schnellladefähigkeit von E-Autos zu optimieren. Zwar können diese Punkte durchaus entscheidend verbessert werden, doch stehen diesen Vorteilen höhere Kosten gegenüber. So ist abzuwägen, ob im konkreten Fahrzeugprojekt wirklich eine höhere Spannungslage erforderlich ist.
Generell wird die höhere Spannungslage ihre Vorteile vor allem bei Hochleistungs-BEVs mit sehr großen Batterien ausspielen können, wo insbesondere die erhöhte mögliche Ladeleistung Bedeutung hat – und seitens der Endkunden auch die Bereitschaft vorausgesetzt werden kann, für die bessere Technik auch mehr zu bezahlen. Bei E-Autos kleinerer Klassen wird die 400-Volt-Spannungslage ihre Daseinsberechtigung behalten; denn außer Kostenvorteilen bietet sie, wie im Vorangegangen dargelegt, noch andere Vorzüge.
Spezifische Vor- und Nachteile von HV-Antriebssystemen: Die Nachteile der höherer Spannungslagen lassen sich technisch beherrschen, aber es ist mit höheren Kosten zu rechnen.
EIN ERFAHRENER HV-BATTERIE-ENTWICKLUNGSPARTNER IST IN JEDEM FALL VON VORTEIL
Um teure Irrwege bei der Konzeption und Entwicklung neuer E-Autos von vornherein zu vermeiden, ist die Zusammenarbeit mit einem kompetenten und erfahrenen Entwicklungspartner wie MAGNA in jedem Fall vorteilhaft – für etablierte OEMs ebenso wie für neu in den Markt der Elektromobilität eintretende Startup-Unternehmen. Mit jahrzehntelanger Erfahrung rund um die Elektromobilität und durch eine Vielzahl aktueller Projekte mit äußerst unterschiedlichen Kunden hat Magna ein breites Spektrum an Expertise im flexiblen Umgang mit den jeweiligen Wünschen und Anforderungen der Auftraggeber. So kann MAGNA den OEM-Kunden flexible Lösungsansätze und Varianten auf Systemebene bereitstellen und die Integration unterschiedlichster Komponenten von Lieferanten aus aller Welt leisten.
Stay connected with Inside Automotive!
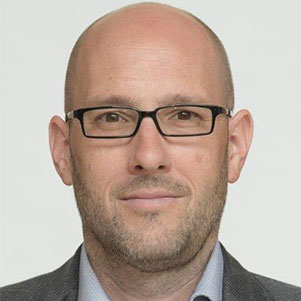
Gerald Gartler
Gerald Gartler ist verantwortlicher Senior Manager für Antriebsstrangmodule und Systemintegration, einschließlich HV-System und HV-Sicherheit. Er begann seine Karriere bei Magna als Konstruktioningenieur für Fahrwerk- und Antriebsstrangkomponenten und arbeitete als Modulgruppenleiter für Antriebsstrang- und Fahrwerksintegration unter Berücksichtigung der Gesamtfahrzeugziele für konventionelle, Hybrid- und BEV-Entwicklungsprojekte.
We want to hear from you
Send us your questions, thoughts and inquiries or engage in the conversation on social media.
Verwandte Stories
Verbunden bleiben
Bleiben Sie informiert und erhalten Sie News & Stories in Echtzeit in Ihren Posteingang geliefert.