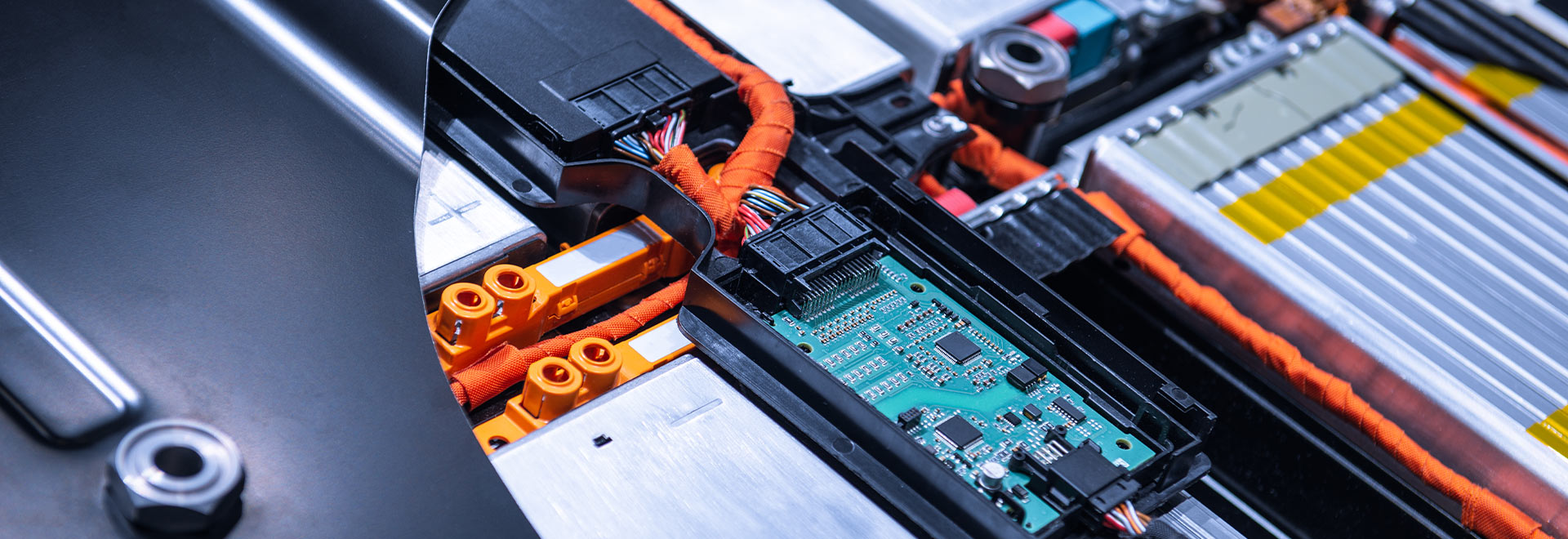
Entwicklung von Hochvoltbatterien für E-Autos – ein
aufgeladenes Thema
- Oliver Heidenbauer
- September 12, 2023
- 6-min read
Die Hochvoltbatterie ist nicht nur die räumlich größte und kostspieligste Baugruppe eines E-Autos. Sie hat auch eine zentrale Schlüsselfunktion für nahezu alle Anforderungen inne, die an ein Elektroauto gestellt werden – von der Performance bis hin zur Sicherheit. Die fertige Hochvoltbatterie ist daher weit mehr als nur ein Gehäuse, in das die Zellen möglichst platzsparend gestapelt werden, sondern ein integratives Element der Fahrzeugarchitektur.
Die Integration der Hochvoltbatterie-Entwicklung ins Gesamt-Fahrzeugsystem eines E-Autos ist somit eine der wichtigsten Aufgaben eines Fahrzeugprojektes. Und die Entwicklung neuer BEVs macht aktuell den weitaus überwiegenden Anteil der Projekte aus, die ein Entwicklungsspezialist in enger Kooperation mit den OEM-Kunden durchführt.
INHALTE DES ARTIKELS:
> Zielkonflikte bei der Hochvoltbatterie – Zielsetzung abhängig von der Fahrzeugart
> Immer ein zentrales Thema – thermische Sicherheit der HV-Batterie
> Last aufteilen – die Hochvoltbatterie als integrale Chassis-Komponente
> Am Anfang war die Zelle – Zell- und Batterieentwicklung laufen parallel
> Vorschriften und Regelungen – der langsame Arm des Gesetzes
> Fazit: Umfassende Erfahrung in allen Entwicklungsbereichen zahlt sich aus
ZIELKONFLIKTE BEI DER HOCHVOLTBATTERIE - ZIELSETZUNG ABHÄNGIG VON DER FAHRZEUGART
Bei den vielen Anforderungen an das fertige Batteriepack ist es kaum möglich, eine einzige als die wichtigste Anforderung hervorzuheben. Schon in der frühen Projektphase müssen in Kooperation zwischen Entwicklungspartner und OEM abhängig von der Zielrichtung des Fahrzeugs – dem Vehicle Target Setting (VTS) – die Hauptanforderungen an die Hochvoltbatterie festgelegt werden. Denn eine reichweiten- und effizienzorientierte Limousine setzt andere Schwerpunkte als ein multifunktionales SUV, ein Kleinwagen andere als ein Geländefahrzeug. Entwicklungsspezialist Magna arbeitet hier üblicherweise anhand von rund 40 Haupt-KPI (Key Performance Indexes), was die Vielfalt der Anforderungen in der HV-Batterieentwicklung erahnen lässt.
Dabei sind oft Zielkonflikte zu lösen: So kann etwa eine möglichst hohe Energiedichte – also viel gespeicherte Energie auf engem Raum – in Widerspruch stehen zu den unabdingbaren Sicherheitserfordernissen, oder die Schnellladefähigkeit kann mit der Lebensdauer kollidieren etc. Die Reichweite wird ebenfalls nicht allein von der Batterie bestimmt, sondern auch davon, wie effizient das Gesamtfahrzeug die bereitgestellte Energiemenge nutzt. Eine sehr große, dafür schwere und teure Batterie erreicht bei ineffizienter Nutzung keine höhere Reichweite als eine kleinere, aber effizient genutzte Batterie. Schnelles Laden ist ebenfalls erst in Verbindung mit einem perfektionierten Batterie- und Lademanagement und einer optimierten thermischen Konditionierung ohne vorzeitige Alterung der Batteriezellen möglich.
Je nach Fahrzeugkonzept kann auch die Sicherheit gegenüber äußeren Einwirkungen mit der Reichweitenoptimierung kollidieren. Für elektrische Geländefahrzeuge muss möglichen Beschädigungen von unten bei Offroad-Fahrten vorgebeugt werden. Das geschieht nicht nur durch Verstärkungen des Gehäuses, sondern auch durch ausreichende Freiräume, damit ein mögliches Eindrücken am Unterboden keine Beschädigung von Zellen, Kühlung oder Dichtebenen verursacht. Dies reduziert natürlich die mögliche Packdichte der Zellen und verringert somit die volumetrische Energiedichte.
IMMER EIN ZENTRALES THEMA - THERMISCHE SICHERHEIT DER HV-BATTERIE
Die thermische Sicherheit der HV-Batterie spielt immer eine zentrale Rolle – nicht zuletzt für die Akzeptanz von Elektroautos. Zu den wichtigsten Aufgaben in der Batterieentwicklung gehört daher, sicherheitskritische Vorfälle am Batteriepack durch geeignete Maßnahmen zu verhindern:
Auf Zell-Ebene muss speziell auf das Thermal Runaway geachtet werden, also das von Übertemperatur induzierte „thermische Durchgehen“ der elektrochemischen Prozesse in der Batterie, was weitere Erwärmung erzeugt.
Auf Pack-Ebene ist es die Thermal Propagation, bei der eine außer Kontrolle geratene Zelle die anderen „infiziert“ und eine Kette von Thermal Runaways auslöst.
Immer wieder geistern Meldungen und Videos von brennenden E-Autos, die nicht gelöscht werden können, durch die klassischen und die sozialen Medien. Diese Geschichten haben den Mythos genährt, E-Autos und deren Batterien seien im wahren Wortsinn brandgefährlich. Empirisch betrachtet ist dieser Sachverhalt allerdings nicht haltbar. Gängigen Studien zufolge entspricht die Wahrscheinlichkeit, dass ein E-Auto zu brennen beginnt, nur einem Bruchteil jener, dass ein Auto mit Verbrennungsmotor (ICE) in Brand gerät.
Bei E-Autos treten gemäß einer Untersuchung am Forschungszentrum Jülich, Helmholtz-Institut Münster, pro Milliarde gefahrener Kilometer zwei Brandfälle auf. Beim ICE sind es etwa 90 Fälle pro Milliarde gefahrener Kilometer. Zwar bezieht sich die Datenlage hier auf eine relativ junge Technologie und damit auf die ersten in größeren Stückzahlen produzierten Fahrzeuge, die gerade erst das Alter von 10 Jahren überschritten haben. Jedoch zeigen die Zahlen, dass die Sicherheit von Battery Electric Vehicles (BEV) mindestens dem Niveau konventioneller Verbrennerfahrzeuge entspricht. Auch die Brandlasten – also die Menge brennbaren Materials – sind entgegen allen Unterstellungen bei E-Autos und Verbrennern sehr ähnlich.
Brandgefahr bei BEV versus ICE
Völlig unterschiedlich ist hingegen der Brandverlauf: Ein Verbrennerfahrzeug brennt sehr schnell aus, sobald sich der mitgeführte Kraftstoff entzündet hat. Ein BEV hingegen brennt langsam, teilweise über Stunden hinweg, weil sich der sogenannte Thermal Runaway nur von Zelle zu Zelle fortsetzt, statt wie beim ICE die gesamte Energie auf einmal freizusetzen. Der verzögerte Brandverlauf erscheint zwar tückisch, ist aber aus Sicht der Fahrzeuginsassen sicherer. Denn selbst wenn der Thermal Runaway einer beschädigten Zelle bereits begonnen hat, bleibt den Insassen mehr Zeit, das Fahrzeug zu evakuieren. Deswegen schreibt eine Gesetzesvorgabe der UNECE vor, dass ab dem Zeitpunkt der Detektion des Thermal Incident mindestens fünf Minuten verstreichen müssen, bis eine Gefährdung der Insassen auftreten darf. Diese Vorgaben werden heute bereits übertroffen: Aktuelle Designansätze gehen sogar soweit, dass es überhaupt nicht mehr zu einem Thermal Propagation Event kommen darf.
Unterschiedlichste Ursachen – der Thermal Incident in der HV-Batterie
Dabei ist nur in seltenen Fällen der gelegentlich als Horrorszenario beschriebene innere Kurzschluss der Zellen Grund für einen Thermal Runaway und im Extremfall für eine Thermal Propagation. Das selbstinduzierte Durchgehen der Batterie kommt ausschließlich von Qualitätsmängeln bei der Batteriezellenproduktion – insbesondere durch Verunreinigungen der Zellchemie. Inzwischen sind allerdings die Herstellungsprozesse erheblich ausgereifter, und somit dürften innere Kurzschlüsse ohne weitere Einflüsse nicht mehr vorkommen.
Es gibt allerdings andere Risiken, die zum Durchgehen einer Zelle führen und die durch geeignete Gegenmaßnahmen verhindert werden können. Dazu zählt eine Verletzung der Betriebsstrategie der gewählten Zelle bzw. der Zellchemie hinsichtlich Temperatur, Lade- oder Entladeleistung. Unter solchen ungünstigen Bedingungen können sich Dendriten bilden. Dabei handelt es sich um astartige Strukturen im Inneren der Zellen, die danach die Separatoren durchdringen und zum inneren Kurzschluss führen können.
Auch die mechanische Beschädigung von außen ist ein wesentliches Risiko, dem bei der Entwicklung und der Integration der Hochvoltbatterie vorgebeugt werden muss. Eine solche Beschädigung kann durch kurzzeitiges Einwirken extremer Kräfte geschehen, wie bei einem massiven Unfall mit weitreichender Zerstörung; oder durch langsame Deformation von außen, etwa durch das Eindringen von Fremdkörpern oder durch das Eindrücken des Gehäuses im Geländeeinsatz. Aber auch von anderen Fahrzeugbauteilen verursachte Brände können die Batterie von außen erhitzen, sodass ein Thermal Incident eintritt. Beispiele hierfür sind Funkenüberschlag durch das Niedervolt-Bordnetz oder Feuer durch brennbares Kältemittelgas der Klimaanlage. Kurzschlüsse außerhalb des Batteriepacks, die den Hochvoltpfad erhitzen, kommen als Ursache ebenfalls in Frage – etwa von den Motoren, von Onboard-Ladern, von DC-DC-Wandlern. Und schließlich können nach längerer strapaziöser Nutzungsdauer Undichtigkeiten auftreten. Auf diese Weise können Feuchtigkeit und Schmutz in die Batterie eindringen, die eine elektrisch leitende Verbindung und damit einen Kurzschluss innerhalb des Batteriepacks herbeiführen können.LAST AUFTEILEN - DIE HOCHVOLTBATTERIE ALS INTEGRALE CHASSIS-KOMPONENTE
Obwohl all diese potenziellen Gefährdungen äußerst unwahrscheinlich sind, muss man sie bereits bei der grundlegenden Konzeptauslegung des Batteriepacks und bei der Batterieentwicklung berücksichtigen. Dazu stellt man auch die Widerstandsfähigkeit der Batterie gegenüber äußeren Einwirkungen auf eine harte Probe. Bei Entwicklungsspezialist Magna werden in der Regel extreme Lastfälle in der Simulation sowie im gesamten Design Verification Process (DVP) nachgestellt, welche die HV-Batterie ohne ernste Beschädigung überstehen muss – also ohne Deformation auf Zell-Ebene, ohne Undichtigkeiten und ohne Funktionseinbußen. Hier ist wieder eine sehr enge Kooperation von Batterieentwicklung und Fahrzeugdesign gefragt. Dies bedeutet, dass das HV-Batteriepack einen essenziellen Beitrag zur strukturellen Gesamtfahrzeug-Performance leistet. Rohbau, Bodengruppe und Batteriegehäuse teilen sich die Lastübertragungen – im normalen Betriebszustand sowie auch im Falle eines Unfalls.
AM ANFANG WAR DIE ZELLE - ZELL- UND BATTERIEENTWICKLUNG LAUFEN PARALLEL
Die Entwicklung der Batteriezellen startet normalerweise lange vor der eigentlichen Fahrzeugentwicklung – auch wenn, abhängig vom jeweiligen Projekt, der Zelllieferant bei Start der Batterieentwicklung schon feststeht. Speziell bei Projekten für größere OEM, die bereits fest mit Zellherstellern zusammenarbeiten oder selbst in die Zellproduktion eingestiegen sind, ist das häufig der Fall. Wenn nicht, muss je nach spezifischen Erfordernissen des Projektes der passende Zellenhersteller gefunden werden. Die gesamte Batterieentwicklung beschleunigt oder verzögert sich dadurch nicht unbedingt. Denn Zell- und Batterieentwicklung verlaufen parallel nebeneinander; die Batterieentwicklung startet nicht erst, wenn die Zelle fertig vorliegt.
Für die Auswahl eines geeigneten Zellherstellers werden in der Regel zuerst auf Basis der Fahrzeuganforderungen mehrere Grundkonzepte entwickelt. Anhand dieser lassen sich die unterschiedlichen Zell- bzw. Zellmodulanbieter vergleichen. So lässt sich die Eignung des jeweiligen Partners aus technischer Sicht für das jeweilige Projekt beurteilen. Nach Auswertung der übrigen Kriterien, wie Kosten, Qualität und Produktionskapazitäten, ergibt sich dann die Empfehlung für einen geeigneten Partner. Dabei ist bei allen Zelllieferanten eine stetige Verbesserung der Zellchemie hinsichtlich Leistungsfähigkeit, Alterung, Sicherheit sowie Kosten zu beobachten. Zusammen mit den Weiterentwicklungen der Zellintegration steigt auch die Energiedichte um rund 10-15 Prozent pro Jahr.
Mit dem Integrationsgrad wächst die Herausforderung
Arbeitete man vor einigen Jahren noch mit Zell-Modulen, die zum Paket kombiniert wurden (Module-to-Pack) ist derzeit die Integration einzelner großer Arrays kombinierter Zellverbünde ins Batteriepack üblich (Cell-to-Pack). Die nächste Stufe, die Integration der Zellen direkt ins Chassis, hat ebenfalls bereits begonnen. Das Ziel ist dabei, die Packdichte der Zellen zu verbessern, um die gravimetrische und volumetrische Energiedichte zu erhöhen. Durch das immer kompaktere Design der Zellintegration wird es aber technisch aufwendiger, Thermal Propagation komplett zu verhindern. Hier werden in Zukunft neuartige Materialien erforderlich sein, die das Übergreifen einer Zellerhitzung auf die Nachbarzellen unterbinden oder zumindest verlangsamen.
Die wichtigste Gegenmaßnahme stellt dabei die übermäßige Wärme einer durchgegangenen Zelle dar, die schnellstmöglich abgeführt werden muss, ehe sie auf die benachbarten Zellen übergeht. Zudem muss der durch die Erhitzung ansteigende Druck geregelt abgelassen werden, bevor er zum Bersten führt. Deshalb sind Abblaseventile (Safety Vents) im Gehäuse erforderlich. Zusätzliche Zellgasleitführungen im Gehäusedesign sind von Vorteil, um die über 500°C heißen Gase abtransportieren, damit sie nicht auf andere Zellen übergreifen können. Außerdem wird in der Zellentwicklung auch an Konzepten der sich selbst abschaltenden Zelle gearbeitet. In dieser werden die elektrochemischen Prozesse bei kritisch hohen Temperaturen unterbrochen, sodass keine weitere Erhitzung mehr stattfinden kann.
Ein auch in Extremsituationen sicheres E-Auto ist immer nur in Kombination mit Maßnahmen an der Zelle, am Batteriepack und am Gesamtfahrzeug möglich. Hier ist es stets vorteilhaft, wenn der Batterieentwickler und der Fahrzeugentwickler unter einem Dach Hand in Hand arbeiten.
VORSCHRIFTEN UND REGELUNGEN - DER LANGSAME ARM DES GESETZES
Natürlich gibt es für Hochvoltbatterien in E-Autos gesetzliche Regelungen für die unterschiedlichen Märkte, die jedoch stetigen Änderungen unterworfen sind. Es ist aber für den Batterieentwickler kaum möglich, sich einfach nur nach den Bestimmungen zu richten, die beim Start des jeweiligen Projektes gültig sind. Denn die Batterieentwicklung ist sehr zeitaufwendig. Je nachdem, welche Ressourcen bereits zur Verfügung stehen – etwa, wie detailliert die Fahrzeugkonzeptentwicklung vorangeschritten ist und in welchem Reifegrad die Batteriezellen zur Verfügung stehen – sind rund drei bis vier Jahre zu veranschlagen. In dieser Zeit haben sich die gesetzlichen Vorgaben meist wieder geändert oder Änderungen stehen unmittelbar bevor.
Deshalb muss der Entwickler den geltenden Bestimmungen immer um einige Zeit vorauseilen und sich informieren, welche künftigen Vorschriften geplant oder in Arbeit sind oder vielleicht bereits als Entwurf vorliegen. Bis diese Entwürfe in bindende Vorschriften gegossen werden, vergehen jeweils weitere Jahre. Einerseits, weil versucht wird, weltweit einheitliche Vorschriften zu finden, aber andererseits, weil die Standardisierungsgremien langsam arbeiten. Doch selbst diese kommenden Vorschriften zu erfüllen, kann unzureichend sein. Ein guter Batterieentwickler wird immer versuchen, die aktuellen und kommenden gesetzlichen Anforderungen überzuerfüllen. Denn das Fahrzeugprojekt wird für einen längeren Zeitraum beim OEM in Produktion bleiben und muss auch dann weiterhin regelkonform sein.
FAZIT: UMFASSENDE ERFAHRUNG IN ALLEN ENTWICKLUNGSBEREICHEN ZAHLT SICH AUS
Auch hier ist ein erfahrener Entwicklungspartner wie Magna von Vorteil. Unerfahrene Batterieentwickler – die immer öfter spontan auf dem Markt auftauchen – legen häufig Konzepte vor, die auf den ersten Blick sehr attraktiv erscheinen. Bei näherer Betrachtung erweisen sie sich jedoch häufig als unrealistisch. Oftmals wird nur die Batterie für sich betrachtet, nicht aber die Gegebenheiten des gesamten Fahrzeugs. Magna hat hier den Vorteil der umfassenden Kompetenz auf allen Gebieten der Fahrzeugentwicklung. So kann man auch im Bereich HV-Batterieentwicklung ohne kosten- und zeitintensive Irrwege die beste Lösung finden.
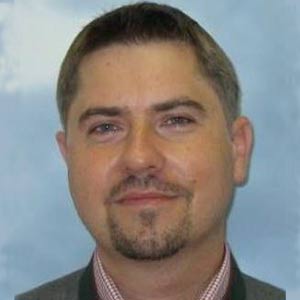
Oliver Heidenbauer
We want to hear from you
Send us your questions, thoughts and inquiries or engage in the conversation on social media.
Verwandte Stories
Verbunden bleiben
Bleiben Sie informiert und erhalten Sie News & Stories in Echtzeit in Ihren Posteingang geliefert.