Battery Enclosures
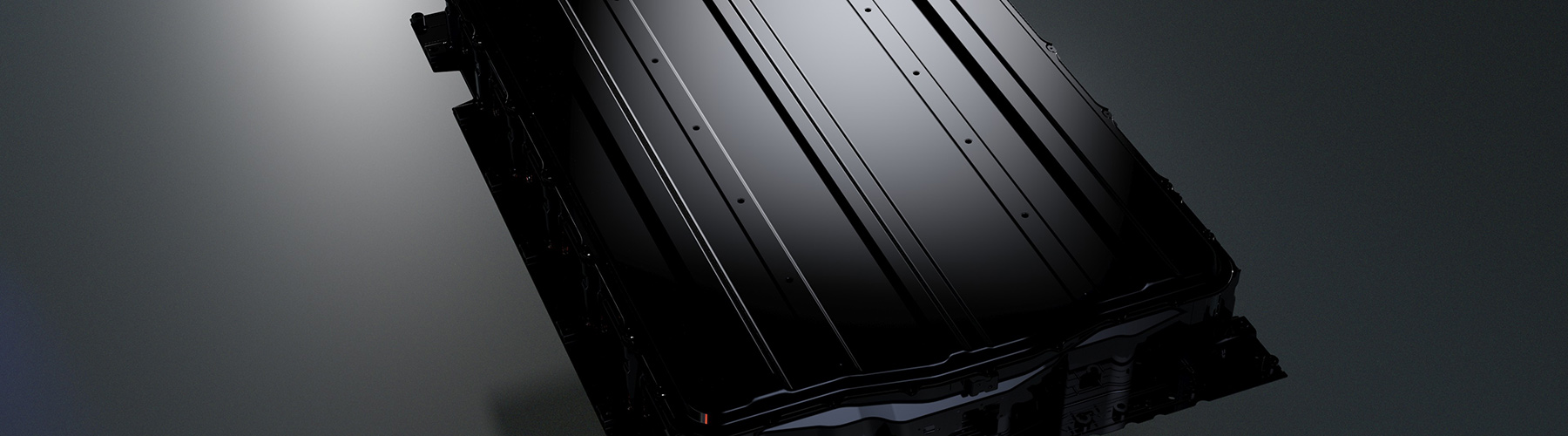
Masters of Battery Enclosure Innovation
Magna began production on two complete battery enclosure systems for fully electric vehicles in North America in 2022. Our first battery enclosure was produced in Europe in 2011 for a hybrid electric vehicle.
Magna provides a comprehensive range of battery enclosure production and engineering solutions, available in steel, aluminum, and innovative one-piece designs. Leveraging advanced materials and cutting-edge manufacturing techniques, Magna ensures optimal performance, safety, and efficiency for electric vehicle applications.
OPTiForm™ Battery Enclosure
Introducing Magna's OPTiForm™ Battery Enclosure, a groundbreaking single-component design, revolutionizing electric vehicle battery enclosures.
Utilizing the innovative OPTiForm™ deep draw stamping process, Magna has created a one-piece tray with near-rectangular corners and sidewalls, enhancing leak tightness and increasing available battery space by 10%. This design simplifies manufacturing and assembly processes, resulting in significant weight savings. Unlike traditional multi-piece designs requiring numerous welds and fasteners, Magna's solution maximizes space efficiency with tight radii, all within an existing stamping infrastructure.
This innovation sets a new industry standard, paving the way for a more efficient and sustainable future in electric vehicle technology.
Steel Capabilities
Discover Magna’s steel battery enclosures, leveraging extensive engineering expertise and advanced forming and joining capabilities.
These enclosures combine the structural advantages of high-grade steel with the cost benefits of lower material expenses compared to aluminum or fiber-reinforced plastic.
Advanced design and manufacturing processes optimize battery space utilization, making Magna's steel enclosures a robust and cost-effective choice for electric vehicle applications.
Aluminum Capabilities
Explore Magna’s aluminum battery enclosures, leveraging our engineering and manufacturing expertise in complex aluminum assemblies.
Offering significant weight savings, Magna’s aluminum enclosures are 20% lighter than comparable steel designs and highly scalable, allowing for the production of various enclosure sizes and designs on a single production line.
Designed as an assembly of extrusions, castings, and stampings, Magna's aluminum battery enclosures deliver top-quality solutions from concept development to high-volume mass production.
Cast Hybrid Capabilities
Since 2011, Magna's Cast Hybrid Battery Enclosure has been a cornerstone in powering next-generation hybrid vehicles. Utilizing advanced cast aluminum alloys that are heat-treated for enhanced strength, these enclosures are produced on high-capacity die casting machines to ensure precision and reliability.
Magna's Cast Hybrid Battery Enclosures are designed to provide robust and reliable housing for hybrid vehicle batteries. Through innovative design and manufacturing techniques, these enclosures aim to enhance the performance and longevity of hybrid vehicle batteries. The use of heat-treated cast aluminum alloys ensures long-lasting strength, making the enclosures highly durable. Manufactured as-cast with no machining, these enclosures offer high-quality dimensions and accuracy. Available in various sizes, Magna's enclosures cater to the diverse needs of hybrid vehicles. Rigorous performance testing guarantees top quality, ensuring that the enclosures meet stringent standards for reliability.
Magna's commitment to advanced engineering and world-class manufacturing has made their Cast Hybrid Battery Enclosures a trusted choice for hybrid vehicle manufacturers worldwide.
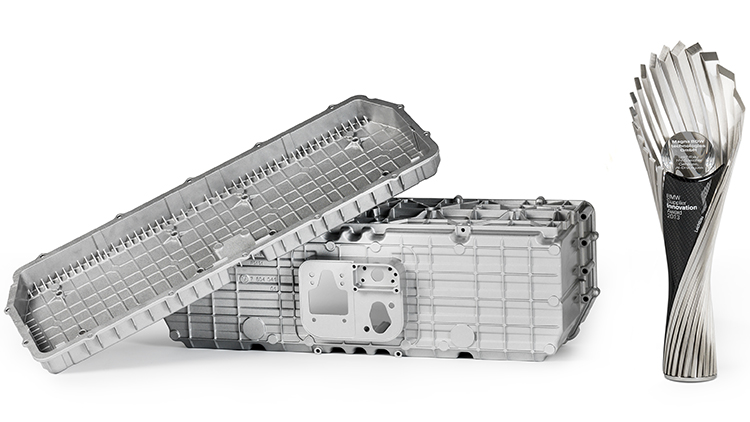