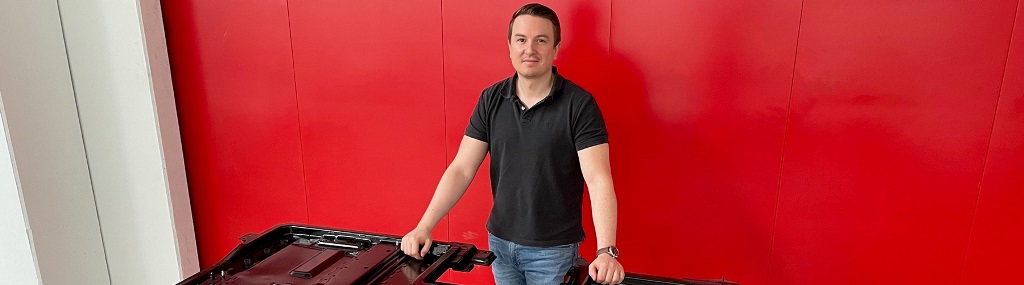
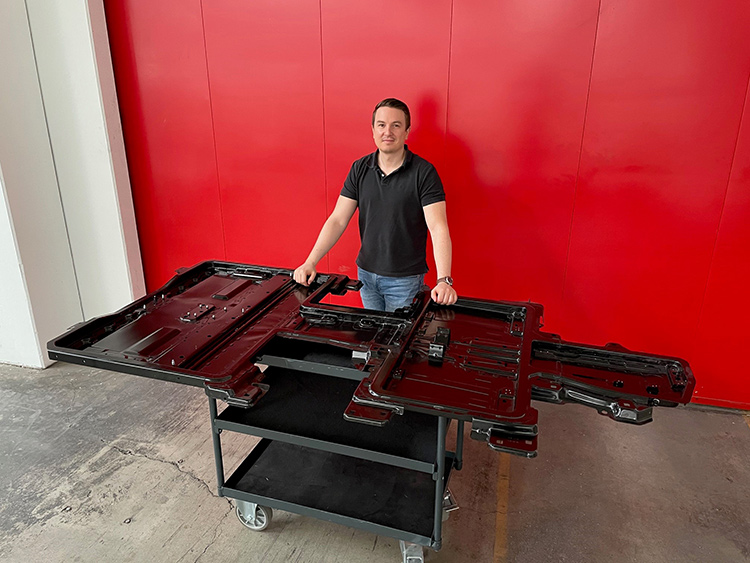
Mein Team hilft dabei, einige der smartesten und innovativsten Fahrzeuge auf die Straße zu bringen, wie etwa den 2022 GMC Hummer EV und den 2022 Ford F150 Pick-up. Ein Technikfreak und „Strukturtyp“ wie ich liebt natürlich die Herausforderung, in einem rasch wachsenden Markt für elektrifizierte Fahrzeuge komplexe Bauteile in höchster Qualität an unsere Kunden in aller Welt zu liefern.
Bei Magna arbeiten wir bereits seit etwa zehn Jahren an der Fertigung von Batteriegehäusen –es begann mit Gussverfahren für Batteriegehäuse von Hybridfahrzeugen. Unsere Expertise in diesem Markt eröffnet Magna große Chancen.
Elektrische Batterien in Fahrzeugen benötigen die richtige tragende Struktur. Diese Strukturen gehen über die üblichen Metallkarosserien hinaus. Batteriegehäuse ergänzen die Struktur und Sicherheit von Fahrzeugrahmen und schützen die Batterien vor Wasser und anderen Schäden.
Dem Endverbraucher bleiben diese Bauteile meist verborgen, die Magna aus Stahl, Aluminium oder Verbundwerkstoffen produziert; sie gehören jedoch zu den größten Teilen in jedem elektrischen Fahrzeug. Die Montage ist eine Herausforderung: Standard- und Laserschweißtechniken müssen eingesetzt werden, bestimmte Stellen müssen lecksicher gemacht oder mit Klebstoffen zusammengefügt werden. Dazu kommt noch, dass jedes Batteriegehäuse einzigartig ist: Es gibt kein One-Size-Fits-All, für jedes Fahrzeug wird ein maßgeschneidertes Gehäuse gefertigt.
Bei Magna arbeiten Entwickler und Forscher rund um den Globus zusammen, um Batteriegehäusekonzepte zu schaffen, die kostengünstiger, leichter und strukturtechnisch besser sind. Unser Systemansatz ermöglicht uns, aus einem großen Pool an Expertise und Ressourcen innerhalb unseres Unternehmens zu schöpfen. Ein F&E-Team in den USA und in Österreich arbeitet zum Beispiel am „BESt Battery Tray“, wobei BESt für „Body Exteriors & Structures“ steht.
Kurz gesagt: Noch ein Traumjob für den „Strukturtyp“ bei Magna.
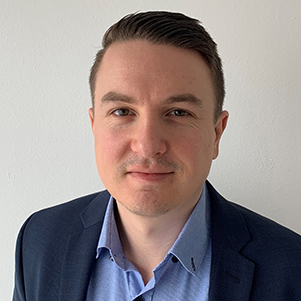
We want to hear from you
Send us your questions, thoughts and inquiries or engage in the conversation on social media.
Verwandte Stories
Verbunden bleiben
Bleiben Sie informiert und erhalten Sie News & Stories in Echtzeit in Ihren Posteingang geliefert.