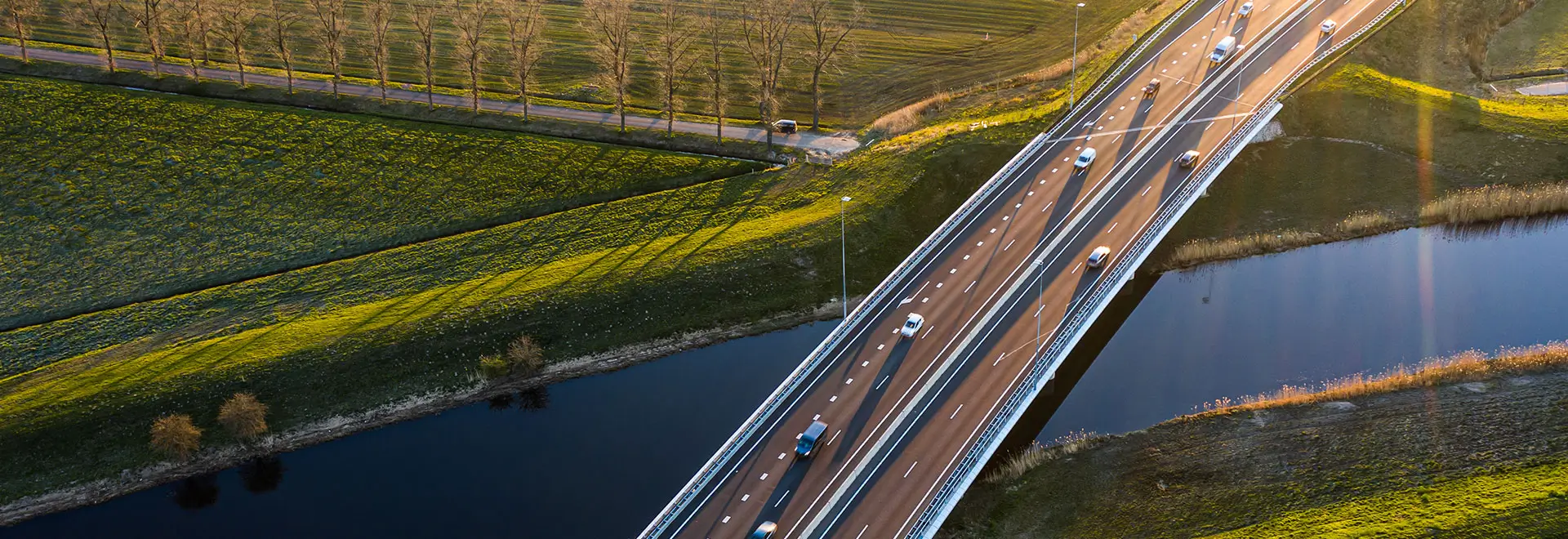
What Makes a Sustainable Car? An Introduction to Automotive Ecodesign
- Dietmar Hofer
- April 13, 2023
- 8-min read
There is no industry in any major market where sustainability has not become a top priority among manufacturers. And in such a globally connected and complex structure like the automotive industry, the consequences of this priority shift are far-reaching. Established vehicle manufacturers as well as new entrants have kicked off extensive restructuring efforts of achieving (almost) net-zero emissions and making the green future a reality.
Such ambitions are commendable, no doubt – but they are also very hard to reach. Sustainability is a highly complex aspect of vehicle planning, and it requires interdisciplinary knowledge and considerable efforts if automotive manufacturers intend to properly integrate it into their business strategy. Most importantly, sustainable vehicle development cannot and should not be seen as a string of singular tasks – every action causes several reactions down the line and no challenge can be solved by one solution only.
What’s ahead?
The aim of this article is to provide a basic overview of sustainable vehicle engineering and production. It covers the essential cornerstones of a holistic sustainability strategy, shows the key aspects of a sustainable vehicle life cycle and explains the major challenges behind a green car.
These topics are explained in detail:
- Key figures regarding automotive industry emissions
- Sustainable ecodesign – the foundation of every automotive strategy
2.1 Dematerialization
2.2 Preventing pollutant concentration
2.3 Substitution/recycling of materials - The life cycle of a green car, which includes 4 areas of interest:
3.1 Material & component design & production
3.2 Complete vehicle production
3.3 Vehicle operation
3.4 End-of-life/recycling - Shifting the burden: Why sustainability is not a collection of single-issue topics
4.1. Avoid burden shifting by developing a holistic view of sustainability
- How Magna supports you with outlining your sustainable car strategy
Keep in mind that this article will not cover all facets of sustainable vehicle production – this topic is too large to allow for a truly deep dive into the matter. In the future, however, we intend to shed light on even more facets of this relevant and incredibly multi-layered topic. So, be on the lookout for more articles.
BEING SUSTAINABLE IN A GLOBAL INDUSTRY – KEY FIGURES
The
automotive industry is one of the largest and most important industries
worldwide, not to mention it being one of the most globalized ones as well. In
2021, over 80 million vehicles have been produced which contributes to about 1 Gt (Gigaton) of
total 49 Gt greenhouse gas (GHG) emissions annually1 – around 2% of all
global GHG emissions. Figure 1 shows a sector-wide detailed breakdown of
industry emissions.
Figure 1: Total global emissions by sector
The majority
of emissions that most current automotive sustainability strategies focus on are
in the transportation segment, which includes all emissions of the actual
vehicles driving on the road. In recent years, there has been an increased
focus on the heat/electricity segment, where most indirect GHG emissions caused
by the vehicle’s manufacturing and automotive supply chain are included.
High
attention is also directed at direct GHG emissions within the industry segment,
that are caused by material production upstream activities and, to a lesser
extent, vehicle manufacturing processes. These emissions must also be considered
for further de-carbonization activities of carmakers.
The automotive industry has started reducing its emissions from complete vehicle manufacturing in recent years. Since 2006, the total emissions from cars produced in Europe have been reduced by around 46% (see Figure 2).
Figure 2: Development of CO2 emissions for complete vehicle manufacturing in EU (Source: ACEA)
But as we will see in this article, there’s still ample potential for optimization – especially during production of materials and components in the entire automotive supply chain (so-called upstream scope 3 GHG emissions). But in short: Sustainability is rightfully considered a key issue in the automotive industry, given how both raw material production and vehicle use create a large amount of GHG emissions. And luckily, most automotive producers and suppliers have pledged to introduce comprehensive sustainability goals into their strategies to steadily reduce total emissions and waste creation across their entire vehicle production chain.
1: Based on average
12,5 tons CO2e per vehicle (raw materials & components
production, vehicle manufacturing, logistics); 12,5 t CO2e/vehicle x
80 Mio. vehicles = 1 Gt CO2e. Average annual total GHG emissions of 50 Gt
CO2e based on published data for net global greenhouse gas (GHG)
emissions acc. latest IPCC AR6, 2023.
SENSIBLE ECODESIGN: THE FOUNDATION OF EVERY SUSTAINABLE CAR STRATEGY
In
automotive development, design is key – that is also true for sustainability. If
vehicle manufacturers want to reduce their carbon footprint, the most effective
way to do so is to focus on sustainable design (or ecodesign) from the drawing board
onwards.
Three
central pillars make up sensible automotive ecodesign.
Pillar #1: How can the resources needed to build the
vehicle be reduced?
The most
direct and generally most efficient way to reduce the emissions from vehicle
production activities is still to keep the resource demands of the vehicle
itself as low as possible. The term dematerialization covers all
measures aimed at delivering the same – or even higher – level of product
quality while decreasing the amount of resources needed to do so. Reducing
scrap rates and optimizing product design for high material utilization are two
main drivers for that.
Keep in mind
that the term “resources” in this sense is not restricted to raw material, but
also includes the energy needed to produce the car and its components as well
as the material needed to operate and maintain the car (primarily fuel/electric
energy). As such, manufacturers should check the energy mix of their suppliers,
as well as use green energy themselves.
Aside from
enabling a higher product output while keeping a constant material and energy
input, reducing resources also means reducing the weight of the vehicle – which
by itself also has positive effects on its fuel/energy consumption rate, and
reduces how often the end users need to refuel or recharge their vehicles.
Pillar #2: How can waste and pollutants be avoided?
The production
and use of a vehicle, even under the most optimal conditions, will produce some
emissions somewhere in the vehicle’s life. And while emissions are colloquially
often associated with GHG emissions, other pollutants are also produced,
ranging from volatile organic compounds and nitrogen dioxide to rubber
particles and packaging waste accumulated during production. One particularly
pressing issue is the concentration
of hazardous pollutants that could potentially harm the vehicle user directly.
To make a sustainable vehicle, the amount of waste should be reduced wherever possible, while harmful substances should be avoided entirely. For example, some vehicle manufacturers have started to use water-based lacquers instead of the common solvent-based lacquers. These water-based lacquers are not hazardous, thus preventing any harm to the health of painters in the manufacturing plant as well as recyclers at the vehicle’s end of life.
Additionally,
ecodesign also focuses on increasing vehicle interior air quality by avoiding
the accumulation of harmful substances inside the vehicle. First, with the application of well-balanced air-recirculation modes in
the vehicle cabin and the selection of appropriate cabin filters, such as HEPA
filters with activated carbon layers. And secondly, selecting low emission
material for the interior compartment also decreases pollutant concentration
inside the vehicle.
Pillar #3: How can primary resources be substituted?
As recycling
grows more and more relevant in the industry, many automotive engineers now
also consider selecting more secondary material in their development strategies
by increasing the percentage of recycled materials used for their
vehicles. This trend has gained additional traction in recent years, as not
only the use of secondary material requires notably less energy, but also
becomes more relevant as new technologies demand resources, which are often
scarce, and as national and supernational circular economy initiatives and laws
emerge.
Additionally,
raw materials can be replaced by more environmentally friendly alternatives entirely,
if possible. For example, in recent years, aluminum has been increasingly used
to replace steel in car bodies, given its significantly lower weight and higher
feasibility to extensively increase the amount of secondary material with it. This
results in beneficial effects on both raw material processing and use phase
energy demands.
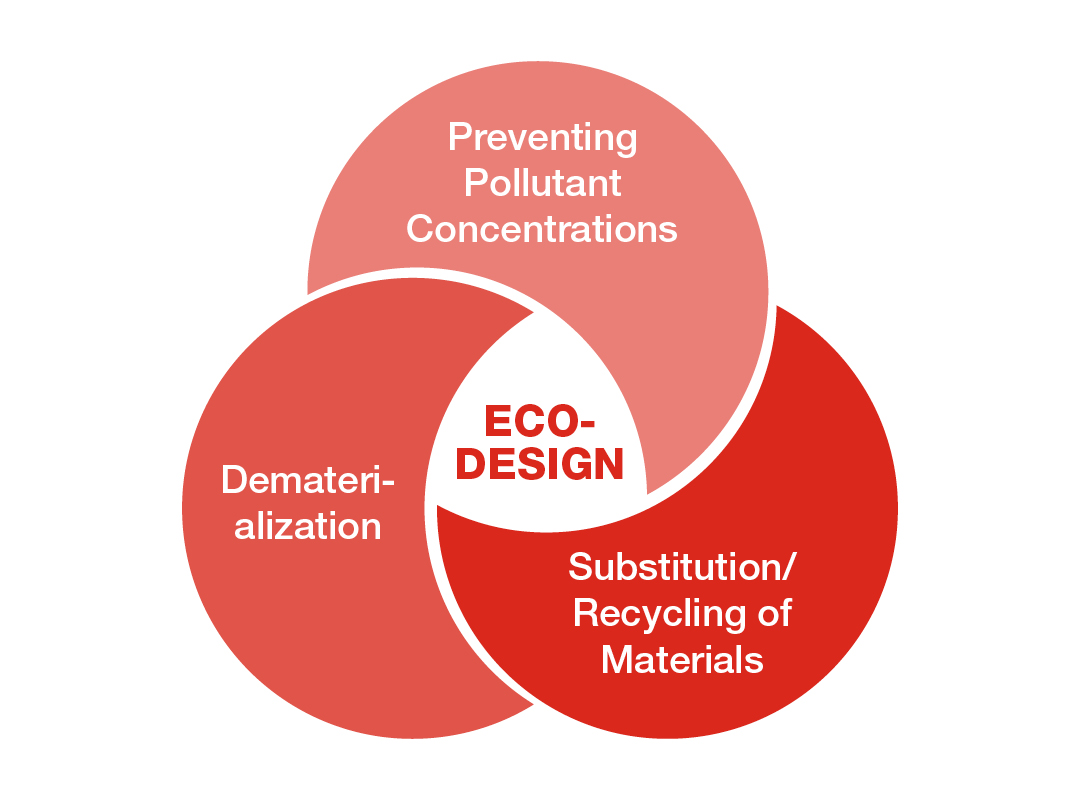
Figure 3: The three pillars of sensible ecodesign
Good ecodesign considers these three pillars at every single decision within the automotive planning process. If an automotive sustainability strategy is going to achieve what it’s supposed to – that is, minimize the negative effects of an automotive company on the environment – the automotive engineers behind the project need a comprehensive plan as well as the knowledge and experience necessary to understand and discover sustainability potential across the entire life cycle of their vehicle.
SUSTAINABILITY IN AUTOMOTIVE: THE LIFE CYCLE OF A GREEN CAR
With the main pillars of a sustainability strategy explained, the next step is to figure out which concrete measures can be implemented during a vehicle’s life. At Magna, we use the following model to separate the average vehicle’s life into four stages.
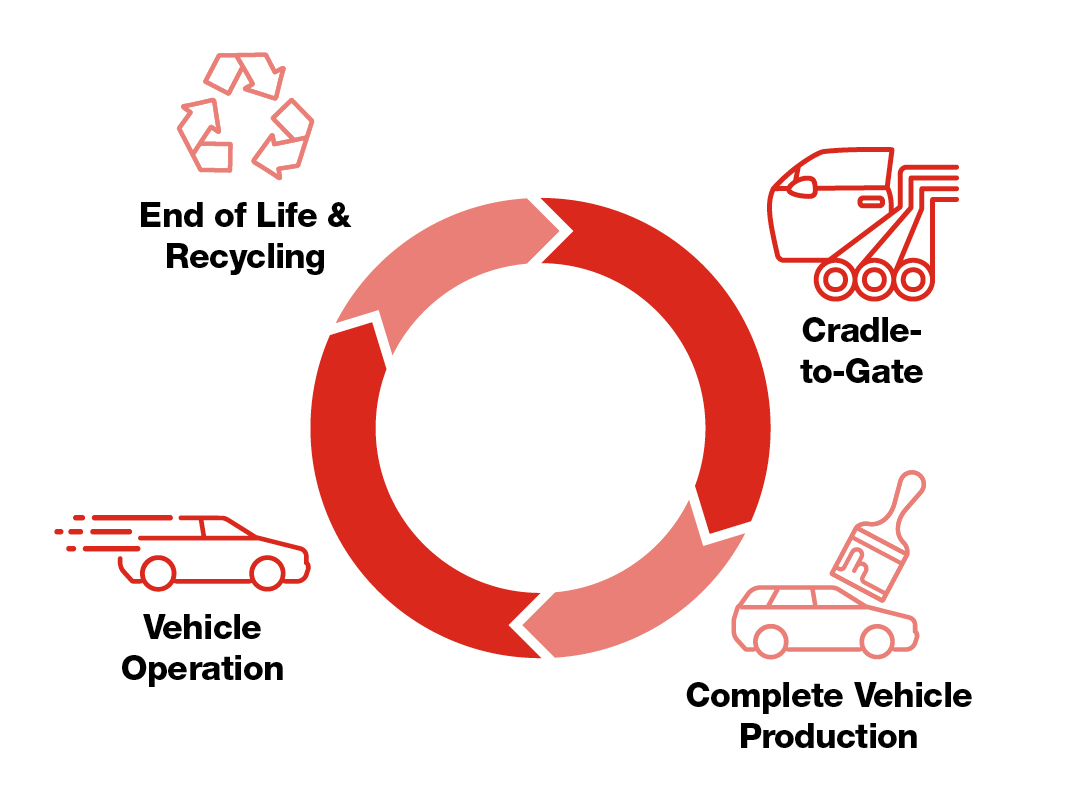
Figure 4: The four stages of every vehicle’s life cycle
Two stages are displayed as larger than the other two. The reason being that during these two stages (Cradle-to-Gate and Vehicle Operation) contribute significantly more GHG emissions than the other two stages (Complete Vehicle Production and End of Life & Recycling)
Let’s take a closer look at those stages:
Stage #1: Material & component design & production (Cradle-to-Gate)
The cradle-to-gate stage covers all steps required to produce the individual components of the car. Producing materials like glass, steel and aluminum; welding body parts; producing chemical precursors and compounding polymers; vulcanizing rubber; excavating rare earth elements; refining special metals; manufacturing cables, semi-conductors, microchips and so on – building a car requires a lot of resources, skills, and energy. Consequently, this stage covers a significant percentage of the emissions created during the automotive life cycle.
There are a lot of options to reduce emissions that automotive engineers can utilize. Substituting raw material with secondary resources or eco-friendlier alternatives; reducing the number of resources needed in general; or seeking alternative energy supply methods for production processes, to name a few.
Additionally, the location of the supplier plays a particularly important role here – regarding the geographical proximity of the partner to the company's own plant on one hand, and regarding local sustainability guidelines and the national energy mix used for local production on the other. Ideally, carmakers should choose local suppliers in countries with a high renewable energy share and strict environmental standards if they want to lower their material and component-related GHG emissions and improve overall sustainability performance.
Stage #2: Complete Vehicle Production
This stage covers the bodyworks, painting, and assembly of individual components into the final vehicle as well as inbound and outbound transport. It is during this phase where vehicle manufacturers can implement sustainability measures most efficiently, given that vehicle production is their core business and all emissions caused during it are under their full control.
Emissions created during this phase primarily correlate to the manufacturing concept of the automotive producer themselves. As such, methods to reduce waste and energy consumption make up a comparatively small percentage of the total vehicle life cycle GHG emissions. But at the same time, manufactures can directly implement measures in their manufacturing sites and achieve net-zero GHG emissions in this area.
We will cover methods to achieve a green factory in more detail in an upcoming article – stay tuned!
Stage #3: Vehicle Operation/use phase
This stage covers the vehicle operation by the end customer, including maintenance efforts. The assumed vehicle lifetime in life cycle assessments (LCA) for average EU vehicles is about 10 years with a milage of 200,000 km – which correlates to a significant portion of total car emissions, especially for ICEs.
EVs perform much better in terms of use phase-emissions, potentially creating close to zero emissions, save for non-avoidable emissions, however, achieving this value requires several beneficial factors. For example, much like in stage 1, net GHG emissions depend on the energy source for charging the car. In countries with little renewable energy production, even the most efficient battery electric vehicle will cause notable emissions.
Again, the work of the engineering team and how they can implement the three pillars of sensible ecodesign is very important – i.e., to improve efficiency and durability of the complete vehicle. They need to make sure that the vehicle can operate for as long as possible, uses as little energy as possible, all while remaining affordable in both purchase and maintenance.
Stage #4: End of Life (EoL)/recycling
In the final stage of the vehicle’s life cycle, the main challenge is how the EoL vehicle and its materials can be returned into a subsequent new vehicle life cycle. Vehicle manufacturers have long since begun to pay more attention to what should happen to discarded vehicles and how the raw materials of the car, which are rare and produced at great expense, can be further used.
Clever ecodesign takes into account that individual components containing critical raw materials for the automotive industry can be easily separated from one another to avoid incompatibilities and other problems for future material recycling. Especially in the case of very complex systems that are composed of a wide range of different raw materials (e.g. the EV´s battery) recycling is very difficult and energy intensive. To reduce high efforts and energy demand for recycling EoL vehicles, manufacturers need to implement a vehicle concept that is dismantling-friendly and compatible with recycling methods.
It is also important to find suitable partners for collecting, processing, separating and re-using target components of the EoL vehicle, followed by state-of-the-art recycling and material recovery methods. Raw materials that can no longer be returned to the vehicle parts production should be recycled in other industries. Of course, the recycling partners themselves should also optimize and further improve their recycling processes and reduce their specific environmental burdens.
Your checklist for sustainable vehicle development
The most important first step to find an effective vehicle sustainability strategy, to be able to identify the greatest potential for reducing a vehicle’s environmental impact, to increase production efficiency, and to improve ecodesign aspects is to ask the right questions. For this reason, we at Magna use an extensive catalogue of questions and checklists to determine the impact and importance of individual sustainability measures. You can check out what this type of checklist looks like by clicking the following link.
BURDEN SHIFTING: THE GREATEST CHALLENGE OF SUSTAINABILITY STRATEGIES
With that, the two key foundations of a product sustainability and vehicle ecodesign strategy are laid out. However, it’s now necessary to invest the time and resources needed for the creation of an automotive sustainability concept to really have a lasting net positive effect. And more importantly, a good sustainability strategy requires the appropriate level of expertise and planning to avoid what we at Magna call “burden shifting”.
In short, burden shifting means that implementing measures to lower emissions in one stage of the vehicle life cycle could cause negative effects in another stage – instead of reducing net GHG emissions, they are simply shifted elsewhere. At worst, the measures can actually increase total GHG emissions, even if the life cycle stage they were aiming at is now “cleaner” than before.
Figure 5: the Life Cycle emissions of an ICE and an EV
The electrification currently happening in the complete land transportation sector is a good thing environment-wise, no doubt about it. After all, EVs produce virtually no emissions during their use phase compared to approx. 116g CO2/km emitted by the average European vehicle. However, sceptics of EVs are correct in pointing out that the electric vehicle’s production depends on a significantly higher amount of special metals (like Lithium, Nickel, Cobalt, or Manganese) and rare earth elements, whose excavation causes notably higher GHG emissions. Also, producing the electricity needed for charging EVs could cause high GHG emissions, if generated by power plants based on fossil resources, i.e. natural gas, oil, and coal. See Figure 3 for a comparison of ICEs & EVs.
Avoid burden shifting by developing a holistic view on sustainability
There are other smaller factors that can also cause negative burden shifting. For example, an assembly concept may not take into account that EV batteries are a complex system by themselves and that they demand a fitting recycling concept. In practice, many of the special metals used for Lithium-ion batteries and rare earth elements used in EVs’ drivetrains are still recycled insufficiently, partly because their complex layout makes it difficult to extract the individual components.
A well-balanced sustainability strategy must consider how changes in one area of a vehicle’s life cycle will affect the other areas. Carmakers need to make conscious decisions about which resources they implement, which suppliers they cooperate with, and how each feature-related decision affects the GHG emission results and recyclability of the final product. If such questions are not answered with a holistic view, then it may happen, that seemingly ecological advantageous decisions in one area simply shift environmental burdens into another area of the vehicle’s life cycle.
https://www.acea.auto/figure/interactive-map-co2-emissions-from-new-passenger-cars-in-the-eu-by-country/
HOW MAGNA SUPPORTS YOU WITH OUTLINING YOUR SUSTAINABLE CAR STRATEGY
While it may
sound simple to take sustainability concepts and implement them into a complete
vehicle, in practice, this is a humongous undertaking, especially for start-ups
and new entrants in the vehicle market. First, the topic of sustainability
itself is incredibly complex.
For example,
reducing the number of resources while keeping product quality, affordability
and safety on the highest levels requires advanced design and engineering
knowledge as well as both the tools and the infrastructure needed to collect
and interpret the data necessary. On the macro level, this article has
primarily focused on reducing the total GHG emissions of vehicles’ carbon
footprint. What it did not highlight however, were the economic and social
aspects of sustainability, which are just as important to consider as the
ecological aspect.
Most
importantly, while the overall targets of sustainability strategies are largely
the same across the entire industry, there is no one-size-fits-all approach as
to which measures are sensible, or even possible for any automotive business.
For this
reason, Magna’s complete vehicle one-stop shop service includes full support in
developing and implementing individual sustainability strategies for our
partners. Courtesy of our long-standing experience in vehicle engineering and
production as well as our pioneering work regarding efficient and sustainable
automotive manufacturing, we have the skills, infrastructure, and manpower
needed to optimize the complete vehicle at every step of its life cycle.
To Summarize:
Let’s recap the key points of this article:
1. Sensible ecodesign in the automotive industry is based on three pillars:
- The amount of resources needed for vehicles in general should be reduced.
- Waste and emissions should be minimized to the lowest possible amount, while hazardous pollutants should be avoided completely in the long term.
- Primary resources should be replaced by secondary resources or more sustainable alternatives.
2. When developing a sustainability strategy, these three pillars need to be applied across the complete vehicle’s life cycle, which consists of four stages:
- The complete process of designing and producing the raw materials and components of the complete vehicle, also known as cradle-to-gate. This phase is particularly important to consider in EV production, as its Lithium-ion batteries are complex and resource-intensive to produce.
- The production of the complete vehicle, including inbound and outbound transport.
- The actual use phase of the vehicle, aka its active lifetime on the road.
- It’s end-of-life stage, where the vehicle is de-polluted, dismantled and its raw materials are recycled to be re-integrated into the life cycle as secondary resources. Again, EV batteries are particularly difficult to recycle.
3. When implementing a sustainability strategy, it’s important to keep the complete life cycle in view. If single life cycle stages are only viewed individually and independent from each other, emissions reduced in one area may simply be shifted into another.
4. Magna can support automotive manufacturers in setting up their sustainability strategy as a part of their automotive one-stop shop service.
Stay connected with Inside Automotive!
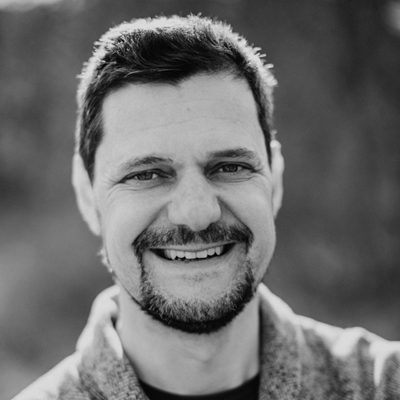
Dietmar Hofer
Dietmar Hofer is Senior Technical Engineer at Magna Steyr Graz. Joining Magna first from 2004-2019 and again from 2020 onward, he has worked as a technical engineer in various roles, including testing, team integration, and environmental protection. He also has extensive experience in ecodesign and sustainability projects, with specific focus on life cycle assessments, recycling, and environmentally friendly product design. He holds a degree in process engineering and has completed additional training in sustainability research, ecodesign and more.
We want to hear from you
Send us your questions, thoughts and inquiries or engage in the conversation on social media.
Related Stories
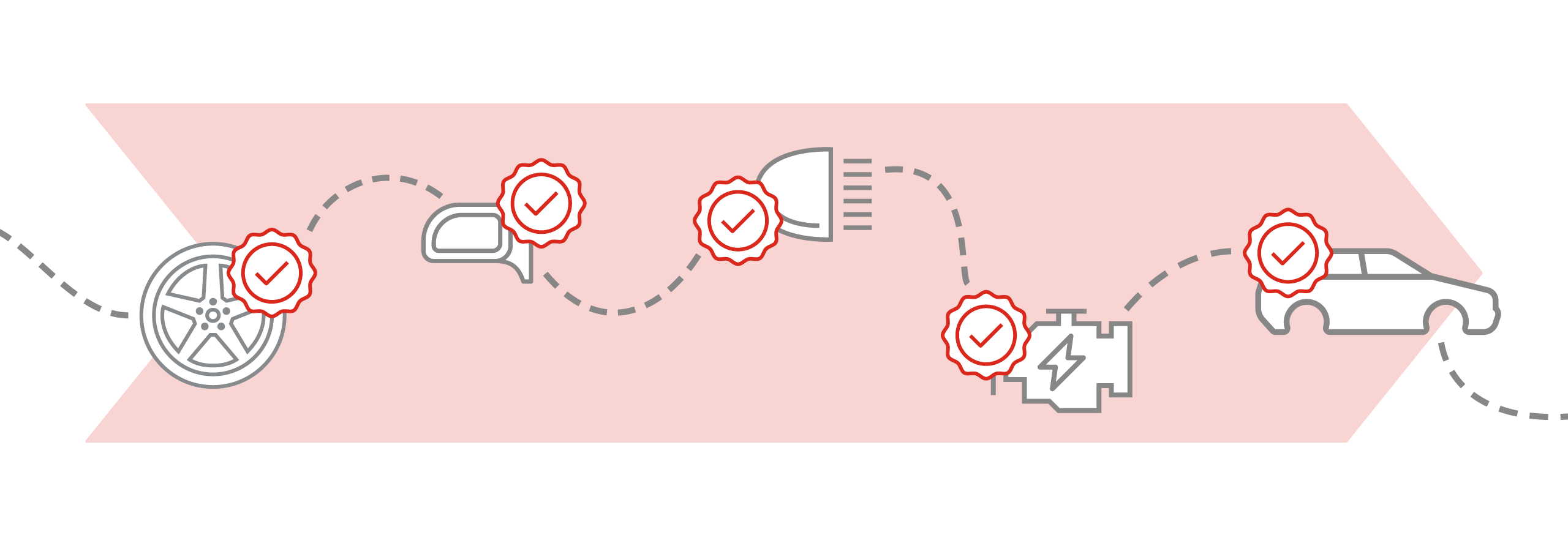
Before Entering the Market, Certification is Required: Homologation for non-European vehicles
Blog
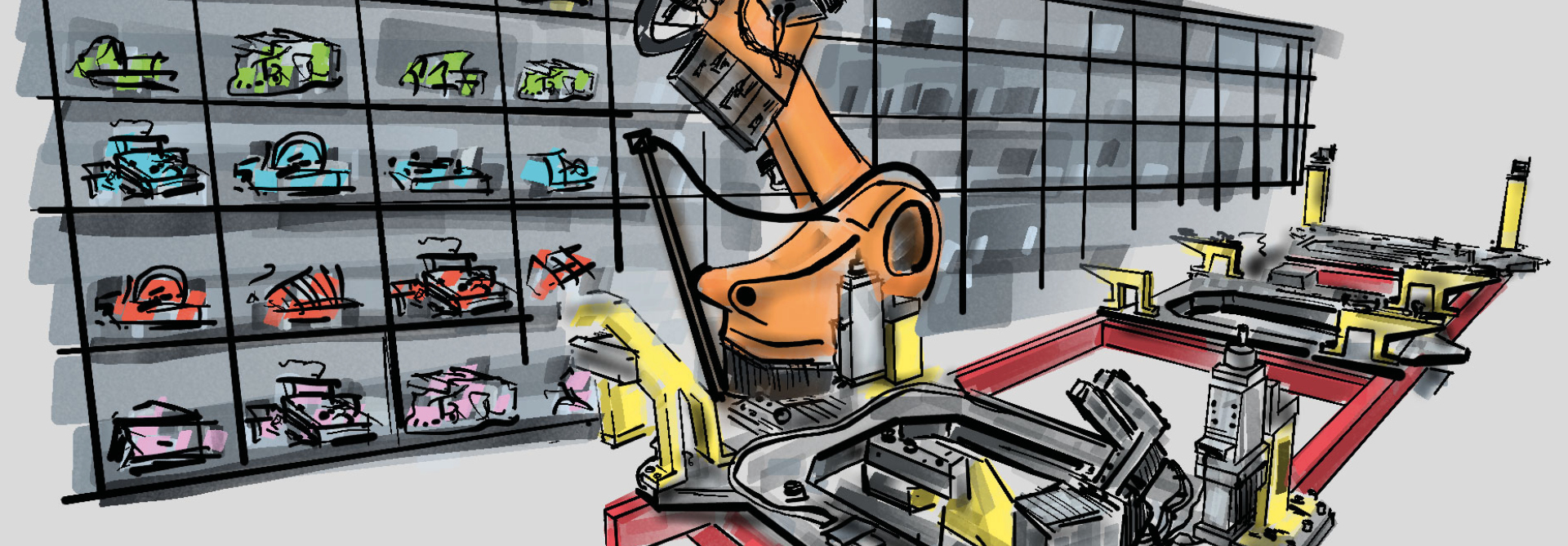
Moving Forward Without Letting Go: How Flexible Manufacturing Advances the Mobility Revolution
Blog
Stay connected
You can stay connected with Magna News and Stories through email alerts sent to your inbox in real time.